How technology can help us become more sustainable
- Like
- Digg
- Del
- Tumblr
- VKontakte
- Buffer
- Love This
- Odnoklassniki
- Meneame
- Blogger
- Amazon
- Yahoo Mail
- Gmail
- AOL
- Newsvine
- HackerNews
- Evernote
- MySpace
- Mail.ru
- Viadeo
- Line
- Comments
- Yummly
- SMS
- Viber
- Telegram
- Subscribe
- Skype
- Facebook Messenger
- Kakao
- LiveJournal
- Yammer
- Edgar
- Fintel
- Mix
- Instapaper
- Copy Link
Posted: 1 March 2022 | Dr Wayne Martindale, Prof Mark Swainson, Tom Æ Hollands | No comments yet
Three experts discuss the future of sustainable product development powered by digital fusion technologies, and how tools such as digital twins can help drive lower emissions and product success.
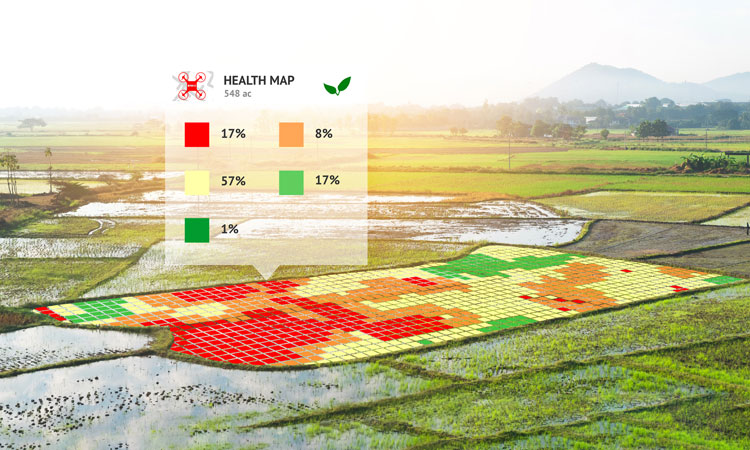
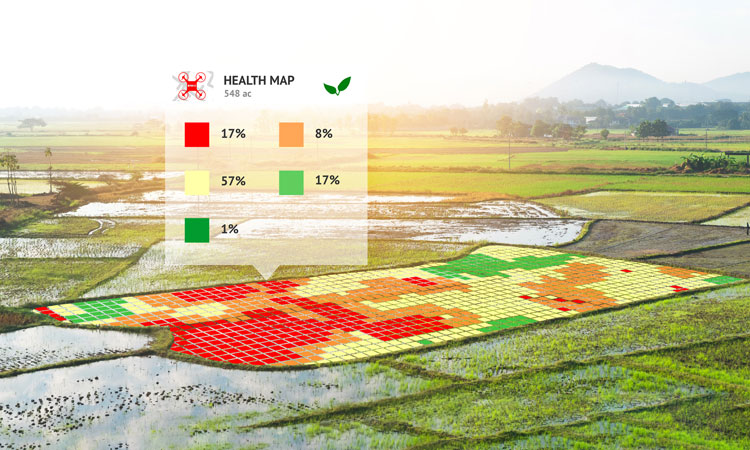
The current generation of food industry professionals is experiencing three epoch-defining paradigms converging in the 21st Century. The first is the advent and fusion of digital technologies – defined as electronic tools, systems, devices and resources that generate, store and/or process data. The defining difference between analogue and digital technologies is that analogue data is converted into blocks of multiple amplitudes, while in digital technology, information is converted into the binary system, where every byte of data is either a zero or one, making the transfer much faster.
The second convergence is the absolute imperative for humanity to ultimately achieve Net Zero, whereby we reach an equilibrium of greenhouse gases (GHG) entering the atmosphere and being removed from the atmosphere.
The final convergence is the rapidly changing nature of our food production/distribution systems and technologies for farm to fork. From strawberry-picking robots, to 3D printed foods, gene modifying/editing technologies and delivery services – the way in which we farm, make and deliver our food is rapidly changing and compounded by the material and energy demands of these systems.
We identify these paradigms as separate strands, changing at different speeds, but they are interrelated and do influence one another. Eventually, as events such as globalisation advance, a convergence occurs where new and existing product development (NPD/EPD) must change and become sustainable. It is through the lens of sustainable product development (SPD) that we explore ways in which lifestyles and quality can be maintained, how they must change and the new frameworks required.
The Booz, Allen and Hamilton (BAH) model
The Booz, Allen and Hamilton (BAH) model was first published in 1982; it was one of the early adopted models for new product development and is still used today. The core foundation of their work manifests in subsequent models and could provide a good starting point for exploring the potential of SPD. However, this was before the emergence of BRIC (Brazil, Russia, India and China) economies and digitalisation, so while the BAH framework is crucial, we must explore necessary changes.
The BAH model is broken down into seven steps:
- New product strategy
- Idea generation
- Screening and evaluation
- Business analysis
- Development
- Testing
- Commercialisation.
Broadly speaking, when seeking to advance SPD, the BAH-based approach to product development will not change; however, the elements that constrain and facilitate this method will require review and adjustment.
For any product being developed, its full product lifecycle must be ensured to equate to an overall balance in emissions, ie, Net Zero. Practical application of this may well result in a carbon cap to new products being developed, or even a maximum ‘carbon pool’ that is depleted through production and augmented by atmospheric extraction. Breaching of the cap would result in a commercial penalty (or toll) and conversely a sustained free capacity in the pool would deliver tax incentives, balanced by the penalty mechanism – a zero sum system.
There will be further associated strategic constraints regarding permitted materials, such as single-use plastics, gases for modified atmosphere packaging, recyclability, water use and potentially provenance or logistical methods – all related to a sustainability strategy.
Changing dynamics for product development
This context – a zero-sum carbon sustainable system – immediately changes the SPD dynamic when generating ideas for products: the home and retail food store are prioritised very differently.
Fortunately, the challenge in selecting appropriate raw materials is facilitated by the first convergence: digital technologies. The supply chain is now increasingly digitally connected, through immutable and trusted datasets, and often underpinned by high performance computers, sensors and interoperable systems. This allows suppliers to offer significant assurances through digital fusion that provide unit-level dynamic data on emissions. This spans from development to decay – eg, those suppliers who are able to provide Net Zero ingredients (or close thereof) will have a greater weighting; this transparency concurrently enables rapid access to food safety, quality and nutrition-related data, providing further benefit and assurance.
Access to trusted, accurate and immutable data is not the only facilitator for the SPD process. Such datasets go beyond the immediate raw materials supply chain to include consumption, weather patterns, product trends, social media, predicted climate impact, water tables and many others – even drilling right down to the immediate town/community-level data the business is based in, and to where the products are sold/consumed. These large and diffused datasets could create a type of choice paradox or herding effect, where the richness and quantity of data is too much for the developer(s) to manipulate. Deployment of a deep learning/AI assistant is therefore likely to become commonplace, as such technologies are ideally suited to manipulating large datasets; and thanks to Moore’s Law, the computational power to utilise them is increasingly cost/time effective to deploy.
The sustainable credentials of the food products become intrinsic to the design process – rather than an afterthought
Hand in glove, the virtual assistant will support the developer in generating new ideas and insights into potential products and associated market opportunities, informed by trusted and immutable datasets, sources and sensors. The ideas generated thus will be subjected to screening and viability assessments by the developers.
At this stage, the model differs from the traditional approach in that it creates a digital twin (a virtual representation of the system/object) for each new product idea.
By implication, this also means that by creating a digital twin for each new product, the process also concurrently establishes the costs (financial and carbon), potential returns and resource availability assessments for each potential new product. In turn, the potential returns are not gross estimations, these can be tempered by utilising datasets within a digital simulation. The simulation can be very broad, accounting for commodity fluctuation modelling and even past product failures. The sustainable credentials of the food products become intrinsic to the design process – rather than an afterthought.
The screening and selection of sustainable criteria could even be taken a step further with the digital twin being immersed within a virtual/augmented reality setting to engage directly with the consumer on its high-level merits and unique selling points. Limited by organoleptic measures, these exploratory proto-consumer engagements would otherwise assist in fine tuning the product. Eventually, a sustainability ‘weighting’ could be assigned to each of the digital twinned new products and, based on the results, a selected proportion of the proposed new products could enter the next stage of the SPD process.
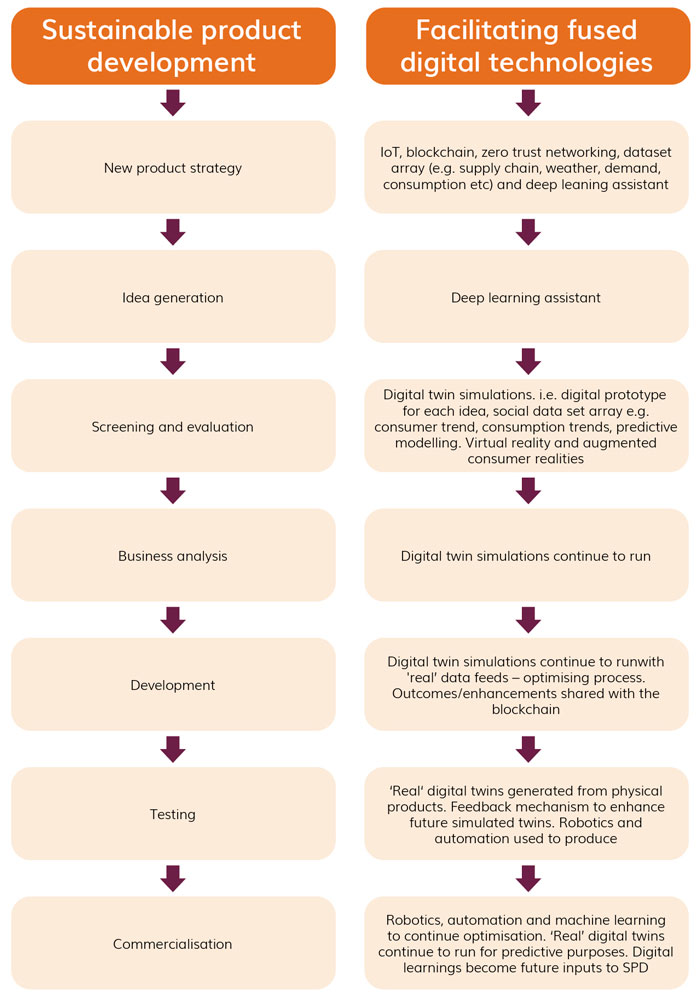
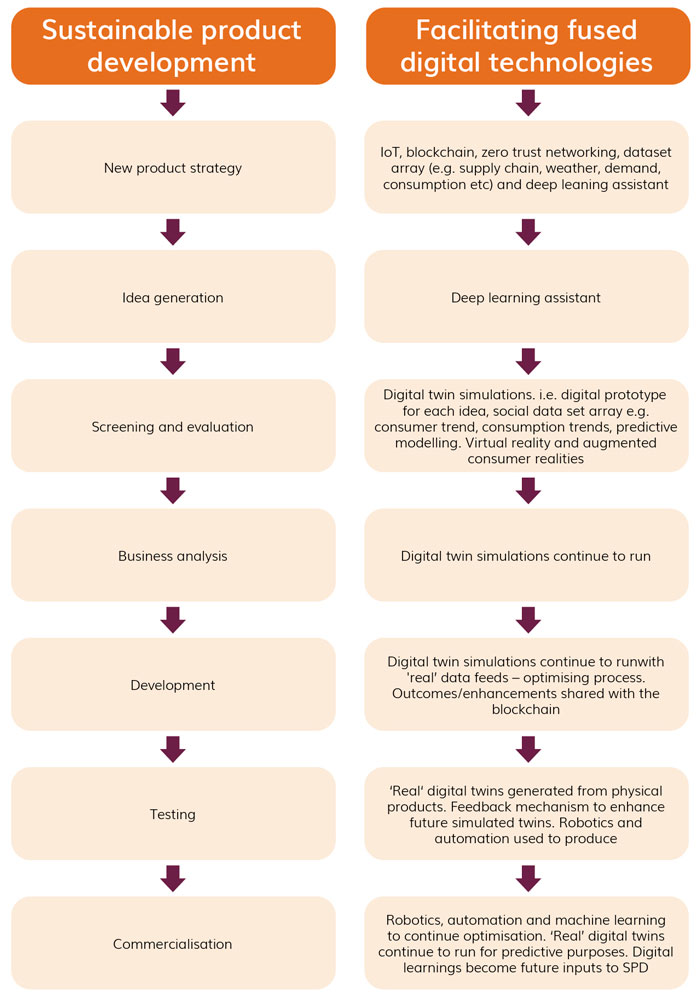
Figure 1: Demonstration of the SPD route map using digitalised technologies
It is important to note that up until this point no food has been touched, tasted or otherwise created to support the SPD process. The digital twinned new products will continue to function in their simulated worlds, using the dynamic data from the supply chain to further simulate the lifecycle of the product and identify weaknesses, threats and potential opportunities. The perspective would not only be limited by commercial considerations, it would also include the emission aspect, such as impacts (and possible failures) of equipment, systems and personnel, and how such circumstances may directly contribute to increased emissions, which out of the simulation would deplete the emission pool and thus reduce value.
Road testing the digital twin
Now finally at stage five of the traditional BAH model for NPD, the food product prototype is assembled – it would be reasonable to assume that regardless of how accurate the digital twin is, a ‘kitchen’ sample would be made for initial developer organoleptic assessment. Developers can then further refine, with product characteristics potentially being changed and then reflected/checked in the digital twin.
Full testing would likely still require a physical trial for personnel familiarisation. During the running of the digital twins, repeated iterative simulations would help mitigate the common development challenge of accurately translating ‘kitchen samples’ when upscaling to the manufacturing process, which is a fundamental requirement for all new products.
By creating a digital twin for each new product, the process also concurrently establishes the costs (financial and carbon), potential returns and resource availability assessments for each potential new product.
Digital twins within the full testing stage of the SPD process can also be compared with the early-stage digital twin, potentially even at a unit level (ie, one per product) or into variation of supply chains and their individual contexts. This feedback will help future digital twins by amending weightings to certain characteristics or emergent characteristics and considerations. The simulacrum products follow along the supply chain mirroring their real-world counterparts; this is achieved by end-to-end sensors at each node in the supply chain, from primary producer to manufacturer, to the retailer and the consumer, and in some circumstances, to recycling and waste recovery plants (but essentially to the end of the product’s lifecycle from an emissions perspective).
The testing could include the commercial, productivity, marketing, emissions, food safety, quality and other metrics as required by the developers. The real-world testing adds confidence to the digital twin simulations and the outcomes those simulations showed; it will help support decision making, but there will be inductive limitations and remaining elements of risk. It is important to note that the digital twin is limited by the types and range of risks introduced to it; therefore, the selected properties will be the only ones addressed by the digital twin, meaning other matters may still require attention by the developers and product trial team. Hence the human developer is critical to this stage of the process, not only to test the product, but also to ensure through real-world application that the learnings are incorporated back into the digital twin if the product proceeds to launch.
There will continue to be a level of supply chain collaboration within SPD and through the interconnected supply chain, developer data (with permission) can be shared to help the supply chain partner optimise process. The more efficient the supply chain, the greater the value that can be extracted from depleting their carbon pools.
At stage seven, the products selected for commercialisation are prepared for launch; digital twins of the product components and assembled products are created; and feedback is once again used to inform future digital twins from launch. The development process formally ends here, but the existing product optimisation will continue. No living system remains in stasis and the system inputs will evolve and change, which will have an impact (either positive or negative) on their sum of emissions. These are created in the continued manufacture of this product that, in turn, depletes the manufacturer’s carbon pool.
Similar to traditional practice, an underperforming product can be brought back into an EPD process for re-engineering; with the benefits of the digital twin, this process can be informed and rapidly advanced in the virtual world prior to final confirmation testing.
The SPD process is a logical inference of a fusion of digital technologies, some aspects of which are already in industrial use, and others which are currently under development at varying stages of technology readiness. In due course, the informed decisions and product design optimisation advantages of SPD will facilitate a sustainable food production system, and ultimately a far more sustainable way of life.
SPD has high potential to progress at pace, driven by the food industry’s need to achieve growth and market advantage, all of which is likely to be secured by serving the increasing consumer expectation of change for the better.
About the authors
Tom is the Innovation and Technical Director at Raynor Foods and an accomplished food scientist who has worked in both government and the private sector. His innovations are focused on sustainability and he has an interest in meta food systems, their emerging technologies and the complex links that connect them.
Mark is Deputy Head and lead for Higher Education and Research at the National Centre for Food Manufacturing. His industrial food manufacturing sector expertise was developed while working in senior technical and operations management roles within the high risk chilled and frozen food industry. Mark progresses industry-based research and works with businesses on bespoke innovative projects to address specific food industry challenges.
Wayne is Associate Professor in Food Insights and Sustainability at the National Centre for Food Manufacturing, University of Lincoln. He leads the Food Insights and Sustainability Research agenda at NCFM, working with food and beverage manufacturers to deliver a carbon neutral or carbon zero food system. He is also a Fellow of the Institute of Food Science and Technology, a science champion for nutrition for the STFC Food+ Network, which all support Early Career Researchers.
You may also like:
- Applications of blockchain technology in the food industry
- Will this new technology revolutionise fish farming?
- Podcast: Episode Four: The challenges of sustainability
- Dairy warms to digital twins
Issue
Related topics
Data & Automation, Environment, New product development (NPD), Product Development, Research & development, Robotics & automation, Sustainability, Technology & Innovation