The food journey – transparency, technology and traceability
- Like
- Digg
- Del
- Tumblr
- VKontakte
- Buffer
- Love This
- Odnoklassniki
- Meneame
- Blogger
- Amazon
- Yahoo Mail
- Gmail
- AOL
- Newsvine
- HackerNews
- Evernote
- MySpace
- Mail.ru
- Viadeo
- Line
- Comments
- Yummly
- SMS
- Viber
- Telegram
- Subscribe
- Skype
- Facebook Messenger
- Kakao
- LiveJournal
- Yammer
- Edgar
- Fintel
- Mix
- Instapaper
- Copy Link
Posted: 19 February 2020 | Vincent Desmond | No comments yet
The challenges of supplier management and risk minimisation are vast. Vincent Desmond, CEO at the Chartered Quality Institute, explores industry best practice and what needs to happen to prevent things going wrong in the supply chain.
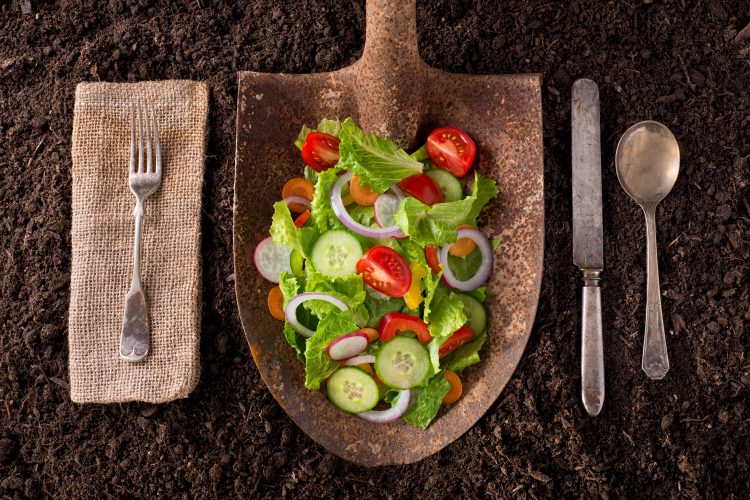
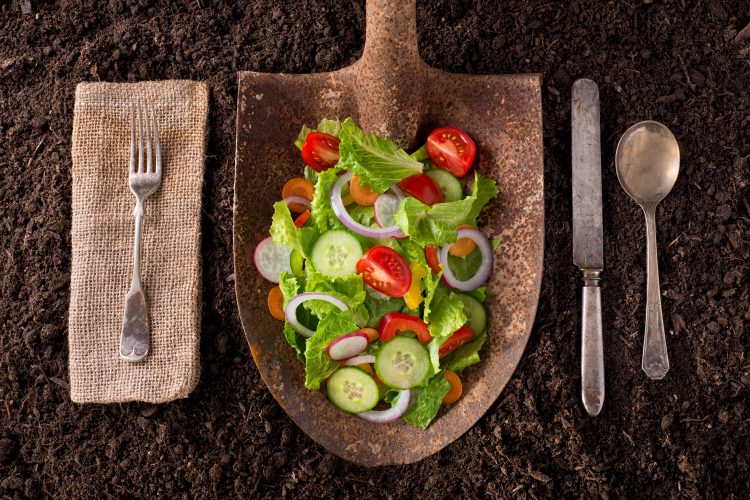
In recent years, a number of high-profile food scares have eroded customer trust. The horsemeat scandal that swept across Europe in 2013 harmed the reputation of several large retailers, while Pret a Manger made headlines in the UK in 2018 after a failure to disclose allergens on their food labelling had fatal consequences.
When things go wrong, consumer-facing businesses such as supermarkets and restaurants often bear the brunt of the blame. But there is more to food than the retailer. Food is a competitive, global business with an international supply chain; on one hand, this has reduced cost and vastly improved choice but, on the other, it has introduced complexity.
The role of regulation and voluntary standards
With complexity comes risk, and when risk is realised in failure the natural response is more regulation and compliance requirements. That is fine, to a point, but regulation by its nature looks backward to realised risk, and fails to anticipate future risk. Who would have predicted fraud in the European meat supply chain?
The UK Food Standards Agency’s (FSA) Regulating Our Future document discusses how developments in the food industry, such as new global players and a changing safety landscape, have necessitated further change to regulation. The current approach fails to consider changing risks, which makes it increasingly outdated and unsustainable. Regulation requires a fresh risk and values-driven approach that keeps abreast of the changing supply chain and allows businesses to adapt their processes accordingly; this way, risks can be addressed at an early stage.
“The defence of ‘we didn’t know’ is not good enough.
There are also voluntary standards and codes that can be applied to the supply chain. These schemes have been growing at pace, but the sheer number of similar but different standards, audits and certificates that the supplier may need to manage creates cost. This is something that the Global Food Safety Initiative has recognised and is trying to resolve, as we need supply chain assurance arrangements that are both effective and efficient.
The major issue with poor regulation and over-standardisation is that it may encourage a compliance mentality and culture, rather than transparency, risk management and, of course, a sense of doing the right thing for the consumer. In this respect, lessons can be learned from the financial sector, which was heavily focused on compliance and regulation, but still managed to do the wrong thing.
Good governance, assurance and improvement
The majority of organisations set out to do the right thing, as expressed in policies and values. However, things continue to go wrong and the defence that ‘we didn’t know’ in such circumstances is not good enough. Society’s view of what constitutes good governance is moving away from the narrow issues of financial performance towards an organisation’s impact, including the supply chain, on all its stakeholders. Consider, for example, the recent changes to the UK Corporate Governance Code 2018, which now includes board accountability for culture and stakeholder requirements.
The questions that food organisations need to address are how to put policy and values aspirations into practice and culture; how they can be sure they are delivering on them; and how they can improve to mitigate risk in their operations and supply chains. The good news is that the closed-loop quality management system provides a method to achieve this, provided it is treated as a strategic, rather than a compliance, tool. The quality management profession is expert in helping organisations translate policy into operational governance or ways of workings; in implementing appropriate business assurance arrangements to de‑risk activity and supply chain, and in helping organisations mitigate risk and drive performance through improvement.
Of course, the magic ingredient in this is ‘culture’, and boards need to send the message that employees and suppliers are not permitted to compromise on quality (and safety is the first quality priority in food); they must accept that getting product out cheap or fast cannot be the first priority for a sustainable organisation. As Robert Bosch – founder of the well-known engineering company – said in 1898, “I would rather lose money than trust.”
Technology and traceability
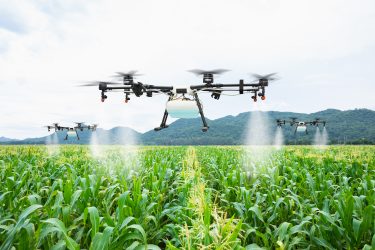
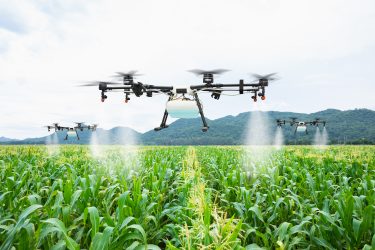
In the future, third-party audits may be more user friendly and forensic, with remote observation of farming and food quality operations implementing drones
Tracing products and ingredients in a complex food chain is notoriously difficult. This has been highlighted by several notable cases, including the instance in which Pret a Manger’s dairy-free yoghurt was allegedly mis-sold by suppliers. In this situation, it was almost impossible to attribute blame because the suppliers denied responsibility, saying that the ‘true cause’ was unknown.
In 2018, following an outbreak of Escherichia coli (E. coli) from romaine lettuce in the USA, issues surrounding the traceability of the lettuce ensued. Much of the produce, contaminated through irrigation systems, originated from multiple sources and most records collected during the investigation were handwritten.
A large proportion of global food companies, 90 percent of which are SMEs, still rely on paper‑based documentation in their quality management systems. However, there has recently been a push for record-keeping to become more standardised. For example, businesses have been encouraged to explore modern approaches to improve traceability through digital records and the use of labels on product packaging.
Audit technologies
The phrase ‘farm-to-fork assurance’ is often used in relation to consumer fears about food origin. As described above, this can be achieved by utilising independent third-party assessment based on voluntary international, sector and company standards. Third-party audits help eliminate the need for individual customer audits, reducing the burden and allowing organisations to refocus attention on monitoring processes and striving for system improvements.
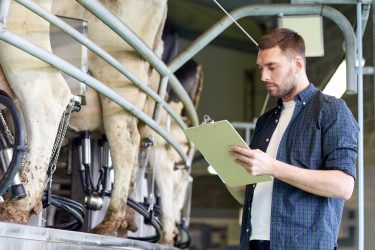
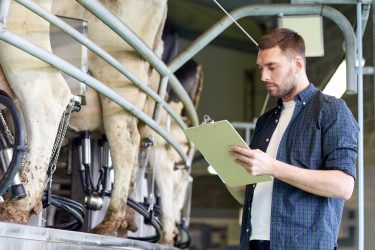
Approximately 90 percent of global food companies still rely on paper-based documentation in their quality management systems
In the future, third-party audits may be more user friendly and forensic. For example, remote observation of farming and food quality operations will use Google-style ‘audit glasses’, ‘audit bots’ and drones. Remote inspection technology will be deployed to reduce the burden of onsite audits, specifically in cases where all that is required are simple checks against existing food safety standards.
Making use of a combination of supply chain digital registers, such as comprehensive supply chain mapping, authenticity testing and risk-based inspection programmes, can provide further management of food safety, leaving little room for opaqueness.
With growing demand from consumers for tighter controls on risks such as allergens, technology will play an increasingly pivotal role. For example, with the use of technology, in the case of Pret a Manger’s dairy-free dispute, the supplier’s denial of responsibility may not be acceptable.
Distributed ledger technology
Potentially, the most game-changing technology in this area is distributed ledger technology or DLT (of which blockchain is an example). This is a digital ledger that uses independent computers to record and share transactions. As it has appeared in different industries, supply chain tracking is a key application. DLT provides point-to-point ownership for food products, giving manufacturers a secure digital record that is necessary for ensuring transparency of raw ingredient origin, where they were processed and sorted, and their sell-by date.
Following bacterial outbreaks, Walmart utilised blockchain to track the origin of leafy green products. Likewise, French supermarket, Carrefour, deployed the technology for many of its products and their ingredients, and their journey from farm to store.
DLT has already started transforming data handling and the way in which quality information is shared by companies. Providing the data is clean and validated, the technology could revolutionise food safety and quality control.
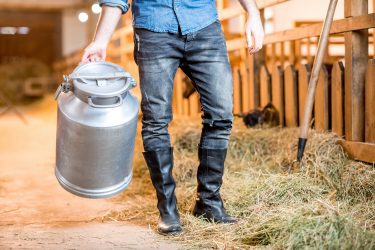
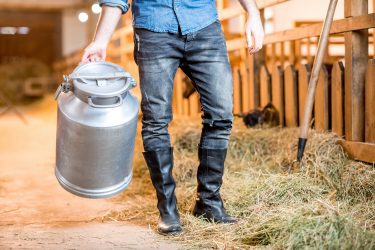
Nestlé has developed a DLT platform that enables consumers to track milk from the farm to producers and independently verify sustainability and supply chain data
Many other large retailers are trialling this technology, including Nestlé as of July 2019. Consumers will be able to track milk from the farm to producers, by utilising a DLT platform, developed by Nestlé itself, to independently verify sustainability and supply chain data.
“We want our consumers to make an informed decision on their choice of products – to choose products produced responsibly. Open blockchain might allow us to share reliable information with consumers in an accessible way,” commented Magdi Batato, Executive Vice President and Head of Operations at Nestlé.
DLT has already successfully tracked the origin of numerous goods from metals through to oils. As well as enhancing milk traceability, Nestlé will use DLT to trace palm oil sourced in the Americas. This comes in response to raised consumer awareness of the deforestation issues surrounding palm oil, and to showcase the brand’s commitment to using 100 percent responsibly sourced palm oil by 2020.
Building trust
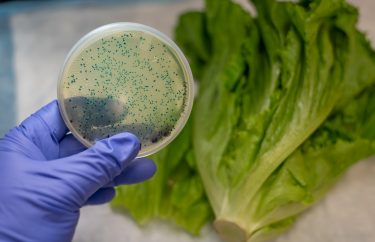
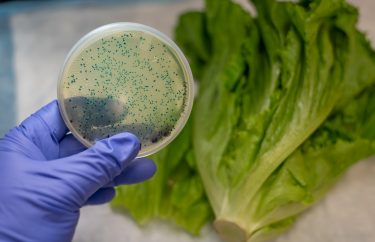
After an outbreak in 2018 of E. coli from romaine lettuce in the USA, issues surrounding the traceability ensued
While technology certainly has the power to mitigate risks, food safety will remain a deeply human endeavour, and culture and relationships will continue to be central to the management of a successful supply chain. To ensure an exceptional standard of quality is maintained within any supply chain, a close working relationship based on trust is fundamental. It is also crucial to nurture long-term supplier relationships to achieve business success.
Historically, the food supply chain has overcome many challenges and it will undoubtedly continue to face obstacles in the future. Good quality management systems and cultures will be critical for creating an industry that is resilient to the ever‑changing nature of the global food chain.
About the author
Vincent Desmond is CEO of the Chartered Quality Institute (CQI), a global professional body for quality management professionals. He is also Director of IRCA Japan, which certifies management systems auditors. Vincent has actively participated in various industry groups, from the UK Institute of Directors’ Good Governance Committee to the International Auditor and Training Certification Association.
Issue
Related topics
Equipment, Food Safety, Research & development, Robotics & automation, Supply chain, Technology & Innovation, Traceability
Related organisations
Chartered Quality Institute (CQI), Food Standards Agency (FSA), Nestlé, Pret a Manger