Portion control is the answer to the food industry’s energy challenge
Posted: 12 May 2025 | David Bean | No comments yet
The food industry’s move towards more sustainable manufacturing techniques alongside ongoing investment into power-hungry assets is placing increasing strain on the sector’s energy supply. David Bean, Business Development Group Manager at Mitsubishi Electric Automation Systems Division, says the answer lies in developing greater flexibility behind the meter.
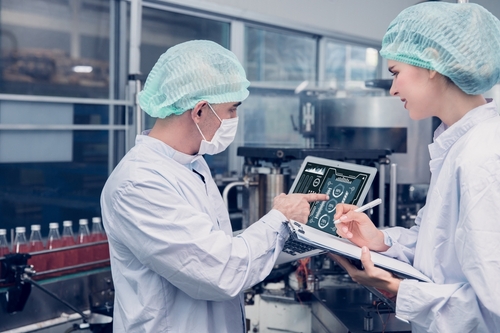
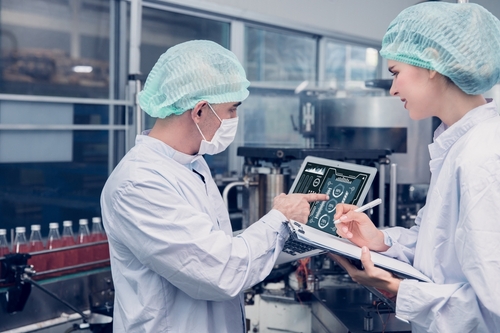
The food industry has traditionally been a heavy energy user, with staple items such as crisps, instant coffee and bread all greedily consuming energy in their production in the form of washing, frying, baking and packaging.
From being heavily dependent on natural gas and electricity – the sector is estimated to account for circa 30 percent of global energy consumption and emissions – it is now embracing more sustainable energy usage in its manufacturing processes.
Rising demand, limited supply
However, the requirement for increased productivity to meet demand from an ever-growing global population places enormous strain on its grid connections and the amount of energy a manufacturer is allowed to use.
The food industry’s shift towards more sustainable manufacturing techniques is vital, but the increasing demand for energy-intensive production processes is placing immense strain on supply.
Attempts to ramp up production are often constrained by supply, with heavy penalties for manufacturers who go over and above their allotted energy supply agreements in the form of demand charges. Those manufacturers who regularly move outside their demand constraints have two options.
The substation route: effective but slow
The first option is to apply for and build a new substation, splitting the energy feed across different subs, or applying for a higher power connection. Unfortunately, the timeline to complete this kind of project can be measured in years rather than months – a timeframe that is too slow to offset an increased number of power-hungry assets at work in a facility and the need for more environmental manufacturing.
The number of power-hungry assets is an important point. All-too-often, a manufacturing site’s power consumption metrics are ringfenced to the shopfloor, but electricity consumption for a site and the potential for penalties now includes distribution, such as new sustainable heating systems that are being transferred from gas boilers to electric heat pumps, or electric vehicle charge points.
Battery storage and smart energy management
A second, and quicker, option is to develop greater flexibility behind the meter with the use of battery storage. This enables a site to insert local renewables into the energy mix, offering the potential of bringing solar photovoltaics (PV) and even wind generation into play.
The concept of peak shift or peak cut is that a site can manage its local grid downstream of the main meter by drawing from a stored battery power supply generated from renewables. During a peak in power demand that threatens to take a site over and above its designed capacity from the local grid, the battery storage can kick in and take the extra load – thus avoiding penalties.
Battery storage offers a quicker, more flexible solution to energy management, allowing manufacturers to better navigate grid constraints and support their Net Zero goals.
All of this sounds relatively simple in theory, but in practice a multitude of different parameters, including different battery systems, grid and market mechanisms must be monitored and balanced in order to deliver a company’s power generation and usage objectives.
For example, a site’s microgrid will need to account for energy prices, asset capabilities and potential revenue generation opportunities from selling surplus energy back to the grid.
All of this information can be used by state-of-the-art energy software, such as Smarter Grid Solutions’ (part of Mitsubishi Electric) Strara Grid and Cirrius Flex software, to effectively manage the behind-the-meter supply.
Such software can detect any trending increase in energy demand before cutting the connection to the main grid from the substation and pulling supply from the battery storage.
The EV challenge and net zero opportunities
But energy management software can go much further. The growth in electric vehicle (EV) sales and the ongoing move towards more sustainable logistics solutions is further exacerbating grid capacity problems.
High power EV charging on a site for a local distribution fleet places significant demand on the local power network. EV charging infrastructure can be paired with solar PV, energy storage and other flexible loads for a complete Net Zero carbon energy and transport strategy.
Distributed energy resource management systems (DERMS) software such as Strata Grid can provide monitoring, controlling, forecasting and optimising across all sizes of site and multiple geographic locations, creating grid interconnection headroom that resolves capacity constraints instigated by factors such as increased EV charging.
Turning constraint into opportunity
Grid constraints are an increasing issue for the UK’s food industry, but as with all challenges they also present opportunities to not only progress the sector’s sustainability agenda, but also potentially generate more revenue.
For more information, you can visit the official website.
About the author
David Bean serves as the Business Development Group Manager at Mitsubishi Electric Automation Systems UK. With over 20 years of experience in industrial automation, he specializes in energy management, digital transformation, and sustainable manufacturing solutions. His insights have been featured in industry publications, where he discusses topics such as energy resilience and the integration of digital technologies in manufacturing processes.