Overcoming the plastic packaging problem
- Like
- Digg
- Del
- Tumblr
- VKontakte
- Buffer
- Love This
- Odnoklassniki
- Meneame
- Blogger
- Amazon
- Yahoo Mail
- Gmail
- AOL
- Newsvine
- HackerNews
- Evernote
- MySpace
- Mail.ru
- Viadeo
- Line
- Comments
- Yummly
- SMS
- Viber
- Telegram
- Subscribe
- Skype
- Facebook Messenger
- Kakao
- LiveJournal
- Yammer
- Edgar
- Fintel
- Mix
- Instapaper
- Copy Link
Posted: 28 August 2019 | Susan Brownlow | No comments yet
As the discussion around plastic packaging and climate change continues, Susan Brownlow takes a look at some innovative alternatives and the state of our current recycling processes.
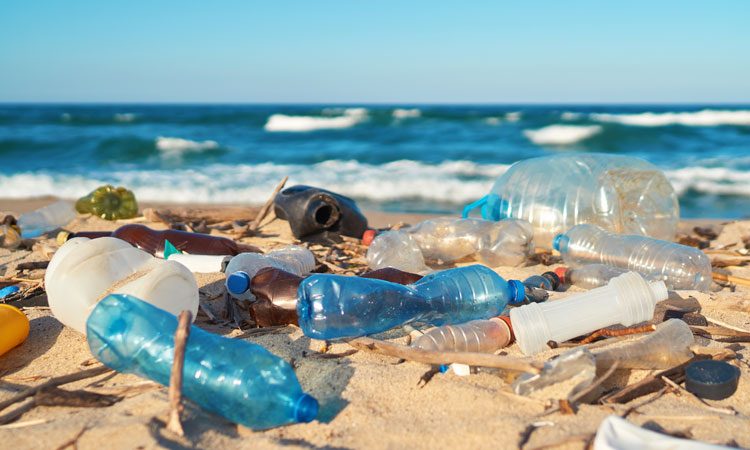
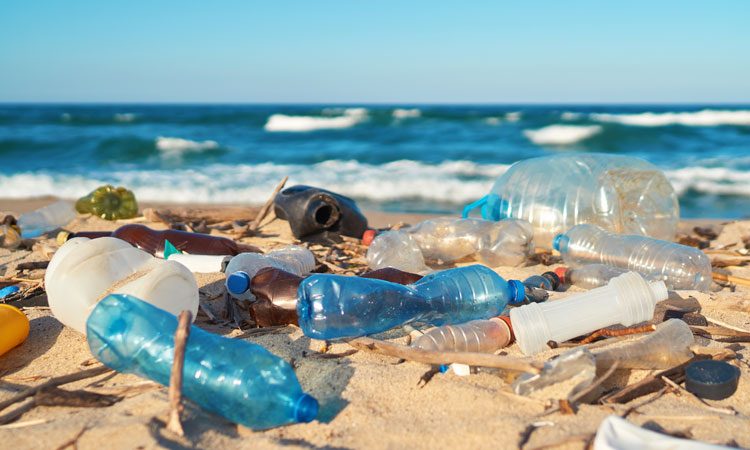
With Tesco recently pledging to intensify its determination to drastically reduce single-use plastic, including measures that de-list brands using excessive or too much non-recyclable packaging, the discussion around plastic packaging alternatives continues to escalate.
Tesco gave suppliers a list of preferred packaging materials last year which included, not surprisingly, sustainably sourced wood, board and paper, glass and aluminium – but also plastics such as polyethylene (PE), polyethylene terephthalate (PET) and polypropylene (PP). In addition to Britain’s biggest supermarket’s efforts to enforce a packaging re-think among its suppliers, it is notable that some plastics remain firmly on their preferred materials list.
With publicity surrounding the appalling level of plastics ending up in our oceans and waterways – and even in our rain, as recently reported in a US Geological Survey, “It’s Raining Plastics”1, there is a significant ground-swell against plastics, particularly those used by the food and beverage industry.
In a report published last year by Kantar TNS, 21% of UK consumers polled indicated they wanted to see entirely plastic-free packaging2.
Adding to consumer concern over the prolific use of plastics, with the rise of technologies to enable viable plastic packaging alternatives, many brands are racing to find and implement plastic substitutions. But is this the only way forward? And with certain plastics on Tesco’s preferred material list, does Britain’s largest retailer know something?
In the last three to four years, there have been exceptional advancements in the development of biodegradable plastic packaging materials – from bioplastics made from corn, mycelium packaging made from mushroom root and sugarcane-based bagasse substitutes for polystyrene to seaweed ‘water bubbles’, wood pulp cellophane and even ‘milk plastic’ – made from ‘casein’, a protein found in milk.
While many of these plastic alternatives will undoubtedly – and deservedly – earn their place in the single-use plastic revolt, one advancement which has garnered rather less attention is the latest process technology to provide a complete recycling solution to mixed waste plastic. Known as certified circular polymers, the process will allow single-use, waste plastic headed for mechanical recycling, destined for landfill or incineration, to be completely re-formed into new plastic products – and repeatedly. This should close the loop on all plastic waste recycling.
Plastics, despite their current pariah image, are immensely valuable and their use has benefited humankind through a myriad of applications. In the food and beverage sector, in addition to helping extend shelf life and prevent food spoilage, plastic materials have even contributed to the environment by improving fuel efficiency through enabling light-weighting in transportation.
Many would argue that today’s issue with plastic waste isn’t entirely about the material itself, but rather our response to it once it has served its initial purpose. With the excessive production and over consumption of short-lived or disposable items – and brands promoting their convenience – our ‘throw-away’ society has, at least in part, turned to mechanical recycling to deal with the mountain of single use plastic. Far from a panacea, mechanical recycling is still very limited to the types of plastic it can recycle, and according to a report by The Guardian3, up to two thirds of plastic waste we endeavour to separate in our weekly collections is shipped to Asia for the recycling to be undertaken.
However, according to Greenpeace in its Unearthed investigation4, startling amounts of UK household plastics have been found in illegal dumps in Malaysia, never having been anywhere near a recycling facility.
New thinking is called for. Hence, an interesting development from an unexpected quarter – the petrochemical industry. Not typically associated with forward-thinking on the environmental front, certified circular polymers are being championed by the world’s largest petrochemical company, Saudi-based SABIC, along with industry partners Plastic Energy, Unilever, Tupperware Brands and Vinventions which develop wine closures to preserve oenolgoic properties.
The breakthrough technology surrounding certified circular polymers will see the recycling of low quality, mixed plastic waste made into a feedstock via Plastic Energy’s system known as thermal anaerobic conversion (TAC). During this process, the mixed plastics are melted in an oxygen-free environment and then broken down into synthetic oils. Once refined, they can be supplied as feedstock for traditional petrochemical uses. Where the technology excels is in its ability to process hard-to-recycle plastics such as polypropylene and polystyrene – including such items as drinking straws, vending cups and meal trays – and both high- and low-density polyethylene items like shopping and bin bags.
The feedstock, TACOIL, is then supplied to SABIC’s petrochemical production plant in the Netherlands to create polymers to be used in packaging solutions across a variety of consumer products. Currently at a pilot stage, small quantities of the circular polymers are being supplied to Unilever, Tupperware and Vinventions to develop high quality – and completely recycled – packaging for foodstuffs as well as personal and homecare products.
As global brand leaders in their respective areas, Unilever, Tupperware and Vinventions are no doubt aware of the mounting pressure for more sustainable packaging and their role in a growing circular economy. They will also recognise, of course, the critical role purity, quality and safety play in food and beverage packaging, but until recently have come up against the safety challenges presented by the mechanical recycling of mixed plastic waste. Unlike circular polymers where the recycling process retains the original polymer composition – so mitigating risk of contamination – recycling by mechanical methods cannot offer the same guarantee.
Announced at the World Economic Forum in Davos at the start of the year, certified circular polymers represent a disruptive innovation and is currently in pilot stage, but with a view to a dedicated production plant scheduled for commercial production in 2021.
While recycling in its current form has been a step in the right direction, for a truly sustainable future, we need to continue the innovative work being undertaken in the area of plastic alternatives from renewable sources. Additionally, we should herald the pioneering technologies that may well enable a fully closed, and potentially infinite, loop for the circular reuse of plastics.
About the author
Susan Brownlow has had three decades of researching and writing on the latest food and beverage technology trends on behalf of some of the world’s most pioneering innovators and is a member of the New Food Advisory Board.
As a tri-national, holding British, American and EU citizenship, she has a truly global perspective on the important issues around food safety and security facing our world today.
References:
- Gregory Wetherbee, Austin Baldwin, James Ranville. 2019. It’s Raining Plastic. U.S. Geological Survey
- Kantar TNS. 2018. Packing Concerns Across Generations.
- Oilver Franklin Wallis. 2018. Plastics Recycling is a Myth: What Really Happens to Your Rubbish? The Guardian. https://www.theguardian.com/environment/2019/aug/17/plastic-recycling-myth-what-really-happens-your-rubbish
- Alice Ross. 2018. Unearthed Report: UK Household Plastics Found in Illegal Dumps in Malaysia. Greenpeace. https://unearthed.greenpeace.org/2018/10/21/uk-household-plastics-found-in-illegal-dumps-in-malaysia/
Related topics
Environment, Packaging & Labelling, Supermarket, Sustainability, Technology & Innovation
Related organisations
Plastic Energy, SABIC, Tupperware Brands, Unilever, Vinventions