Three ways to reduce water usage
- Like
- Digg
- Del
- Tumblr
- VKontakte
- Buffer
- Love This
- Odnoklassniki
- Meneame
- Blogger
- Amazon
- Yahoo Mail
- Gmail
- AOL
- Newsvine
- HackerNews
- Evernote
- MySpace
- Mail.ru
- Viadeo
- Line
- Comments
- Yummly
- SMS
- Viber
- Telegram
- Subscribe
- Skype
- Facebook Messenger
- Kakao
- LiveJournal
- Yammer
- Edgar
- Fintel
- Mix
- Instapaper
- Copy Link
Posted: 8 October 2021 | Amanda Scott | No comments yet
On the back of a fascinating webinar presented by Amanda Scott, SUEZ has provided a crucial guide to food and beverage manufacturers to get more out of the water they use and continue to drive sustainability efforts.
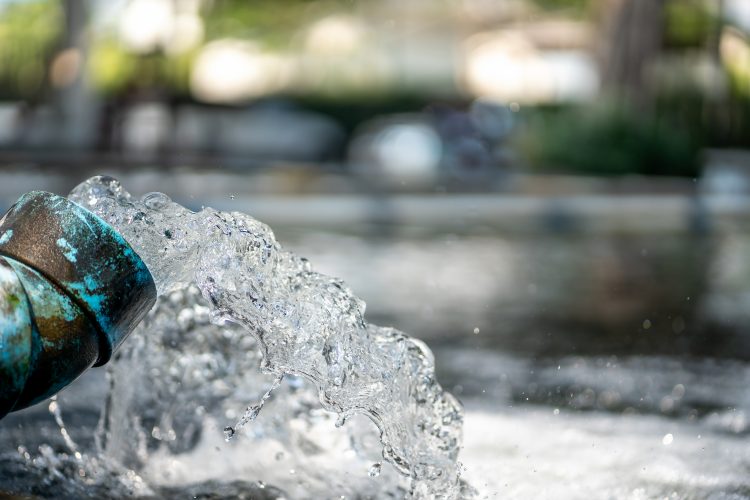
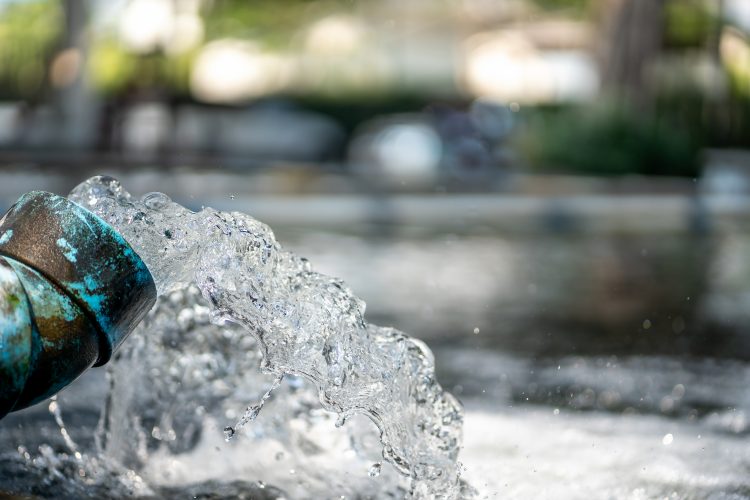
Customers and corporations are pushing for sustainable actions to be taken across industries. At the core of this environmental stewardship is how we manage our water resource. There is no alternative to water like there is for energy. Some areas of the world have too much water, but it is polluted, and other areas of the world have too little and fight for a piece of the resource. Industry requires massive volumes of water in manufacturing processes, from being used as an ingredient, conversion to steam and driving processes, as well as its use in cleaning.
In addition, consumers are seeking brands and products from corporations that have strong sustainability practices and a commitment to environmental protection. All of this has been met with a disrupted supply chain due to COVID-19 and competition for alternative products, so manufacturers must drive internal efficiencies to keep up with changing demand and meet environmental goals.
One key sustainability goal is to reduce water use or enable water reuse. Because it is in such high demand, smarter decisions need to be made with regards to water and wastewater use and treatment. There are three key ways that manufacturers can drive process efficiencies that also save on water use: improving cleaning, reducing wastewater load, and enabling on-site water reuse.
Improving cleaning
Food and beverage manufacturing is largely a batch-driven manufacturing process. Whether from one batch to the next or one product to the next, equipment is constantly in flux, and cleaning is critical.
Cleaning is what ensures product quality and consumer safety. Cleaning is often managed by over-cleaning or simply based on time and consists of rinsing and repeating which consumes enormous amounts of water. Cleaning processes are often multi-stage involving acid, alkaline, and rinse steps. Most cleaning verification is done through visual inspection or sometimes through specific contaminant testing like an allergen or even offline microbial testing. These methods are inefficient or insufficient – they either take too long, are indefensible, or don’t provide a comprehensive view of cleanliness, thus put quality and safety at risk. This is where data can be key. When data is obtained and used to verify cleanliness, not only is the quality and safety of goods protected and defensible, but smarter decisions with regards to water use can be implemented. Optimising clean-in-place cycles with real-time data leads to smarter, more efficient water use and can reduce the amount of water used for cleaning.
Reducing wastewater load
Wastewater management is often an afterthought for food and beverage manufacturers. It is associated with plant costs instead of product — the revenue generator. Because of the batch process, wastewater loading often varies from batch to batch and product to product or is dependent on demand for production. These variations make it challenging to manage wastewater treatment processes to ensure effluent quality is met and avoid discharge penalties.
Often, equalisation tanks are used to manage the changes in load, or measurements of loading are sent to a third-party lab for multi-day testing. These procedures can be helpful to a certain point, but if overloaded and with no valuable data about quality, plants may need to haul off waste, upset treatment, or even discharge unfit water into the environment. Additionally, if wastewater load increases unexpectedly, it could mean there is an issue with the process or potentially cause product loss. These issues can be countered by proper monitoring of production processes to avoid leaks, upsets, or excursions. Monitoring leads to understanding the wastewater load which in turn allows operators to make smarter and faster decisions whether to retain, to divert, or, if suitable, to discharge. Discharging clean waste instead of hauling off wastewater can result in significant resource and cost savings.
Enabling on-site water reuse
With so many different uses of water required at a manufacturing facility and through onsite water treatment, there are several opportunities to treat water for potential reuse. Some uses of water, as in food and beverage ingredients, require the water to be very pure, but other uses such as washing, or irrigation do not require high quality water.
With processes in place to treat and recycle, there are several water reuse opportunities, ranging from collecting and polishing return condensate, treating membrane reject, and collecting rinse waste, to name a few. Reuses could include boiler feed, cooling tower makeup, clean in place pre-rinse, or even potable water. When the treatment is available, and the water is prime for reuse ―and as long as it is not contaminated enough to be considered waste ― a plant can strive for water neutrality across the facility. Determining the quality of water helps drive decisions for proper and safe water reuse.
Optimising water use throughout production and cleaning is critical for product safety and consistency. Enabling on-site reuse, reducing wastewater load, and improving cleaning are three ways to reduce water use in food and beverage manufacturing. Using total organic carbon (TOC), a comprehensive way to view organic contamination or lack thereof, as a parameter can measure any remaining contamination levels, verify equipment cleaning, and determine whether the water is fit for reuse. Proper monitoring and proactive process control with TOC data helps alleviate product recalls, wasted product, downtime, and provides opportunities to reclaim onsite.
There is no alternative resource to water, and manufacturers and consumers alike are pushing for ways to better manage it through conservation, improved treatment, and smarter use where the quality matches the purpose. These sustainability efforts not only drive costs down, increase efficiencies and improve processes, they also be used in marketing campaigns to enhance a brand’s image and reputation.
About the author
Amanda Scott leads the industrial and environmental product team for the Sievers brand of TOC analyzers by SUEZ-Water Technologies & Solutions.
In this role, Amanda develops and supports innovative monitoring solutions to help industries and municipalities meet their quality, compliance and control goals. She has been published in a range of trade journals and has presented at 20+ different national and international water conferences.
Amanda has a Masters in Chemical Engineering from University of Cambridge and a Bachelors of Chemical Engineering from Vanderbilt University.