Industry 4.0 and the food and beverage industry
- Like
- Digg
- Del
- Tumblr
- VKontakte
- Buffer
- Love This
- Odnoklassniki
- Meneame
- Blogger
- Amazon
- Yahoo Mail
- Gmail
- AOL
- Newsvine
- HackerNews
- Evernote
- MySpace
- Mail.ru
- Viadeo
- Line
- Comments
- Yummly
- SMS
- Viber
- Telegram
- Subscribe
- Skype
- Facebook Messenger
- Kakao
- LiveJournal
- Yammer
- Edgar
- Fintel
- Mix
- Instapaper
- Copy Link
Posted: 1 September 2017 | New Food | No comments yet
Industry 4.0 is the development of manufacturing technologies that enable higher levels of interconnectivity, leading to greater communication between machines and decentralised/local processing of data. The result is smart factories in which machinery is increasingly autonomous, with the ability to manage its own service and maintenance requirements and adapt instantly to new production requirements. Mitsubishi’s Garry Lewis explains how this could impact the food and beverage sector.
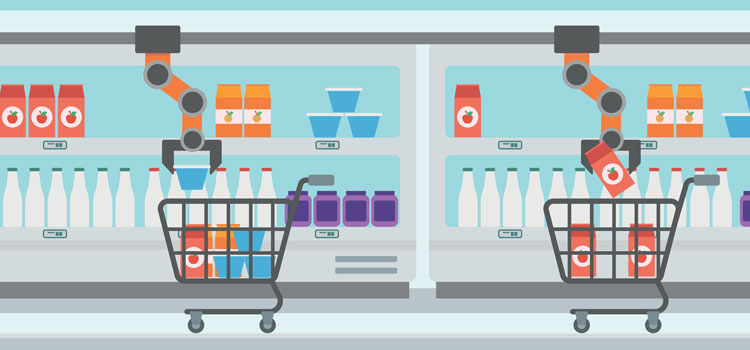
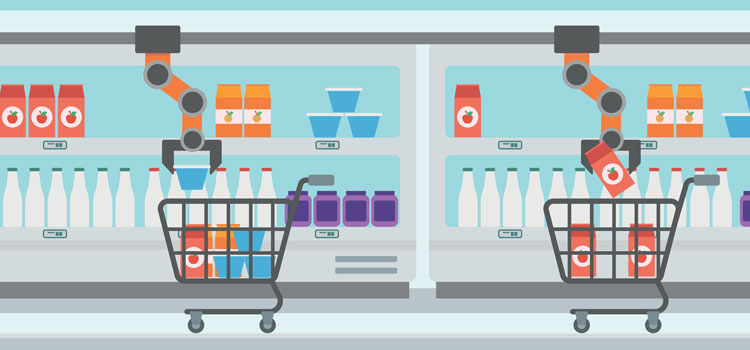
There are plenty of people who consider Industry 4.0, and the digitalisation of the manufacturing sector, to be the coming of the next industrial revolution – though most consider it more of an evolution than a revolution.
Incorporating a plethora of industry trends including, but not limited to, the Internet of Things, the Cloud and big data, it is not so much a ‘thing’ as a movement made up of any number of things. How will this change and benefit the food industry?
Food and drink, as is well known, is the UK’s largest manufacturing sector. Despite this, or perhaps because of it, margins are relatively small and machinery is very expensive. The opportunities provided by the digitalisation of manufacturing therefore need to be carefully evaluated before companies will be willing to embrace them.
However, once the benefits are demonstrated to the industry then Industry 4.0 has the potential to be swiftly implemented across the sector. The constant pressure on costs in the food industry means it has a long history of innovating, so is likely to embrace Industry 4.0 quickly and enthusiastically.
Some aspects of the Industry 4.0 revolution have already become widely accepted. For example, the need for traceability right through the production chain has already ensured that machines are interconnected and archiving data. Industry 4.0 is set to enhance this. Greater flexibility will enable bespoke production for each customer and rapid adaption to changing product specifications and energy usage can be monitored and optimised to new levels.
Connected and communicating production machinery and supply chains will reduce wastage, enable more flexible production with shorter swap-over times, and provide greater energy and machinery utilisation transparency, thus improving Overall Equipment Effectiveness and other key performance factors.
Systems and components that exchange information to control and regulate themselves will considerably increase the potential for leaner production. Depending on the product and manufacturers’ individual business models, additional benefits, such as mass customisation or expansive cloud-based track-and-trace capabilities could be offered. Some consider the term Industry 4.0 to be vague or interpret it in different ways, but regardless of this it will have a significant impact over the next five to 10 years.
The net result will be improved machine performance, optimised maintenance and reduced costs. This should help win new customers and retain existing ones. It is also likely to create new revenue streams in the form of value adding services, and allow seamless connectivity with upstream and downstream supply chain partners.
Significantly, Industry 4.0 is not just a ‘big boys’ toy’. If anything, it offers even greater opportunities for small- and medium-sized food and drink producers, who will be able to form seamless links with their machine builders and technical services suppliers. This will advance and enhance the sophistication of their production systems to the levels of their larger brethren.
For instance, it will permit the optimisation of preventive maintenance programmes, so that expensive and delay-inducing machine failures are all but designed out. Put another way – the overall equipment effectiveness (OEE) strategies that have hitherto been the preserve of larger companies, will come within reach of all.
We can sum up Industry 4.0 as improving data management through better communication and data collection across all machines in the production chain; instant archiving and data historian functions; real-time analytics; multifunction alarm management; web-publishing; as well as interconnectivity and data transparency throughout the entire value chain.
Most engineers are able to see the practical advantages that the new cyber-physical interface of Industry 4.0 will bring. However – like the internet 20 years ago, or mains electricity 100years ago – it will almost certainly over-deliver on expectations by orders of magnitude. This is because while we can foresee the immediate and obvious benefits, far more will almost certainly evolve over time.
Naturally, to feel the full force of Industry 4.0’s benefits, the industry will require its men and women to adopt it enthusiastically. Though there is always some measure of scepticism to any change, once people understand and experience the advantages this revolution could bring, they will support it.
The automation, increased digitalisation and connectivity might, at a glance, sound threatening to the human workforce. However, as with all past breakthroughs new skills will be developed as a result of any upheaval and the change will have to be managed. This move, if handled correctly, will be critical to fully realising the potential of Industry 4.0.
People working across the industry – from manufacturing to research and development – are constantly looking for ways to improve performance and streamline the entire production process. Improved measurement methods, sensors and instrumentation can only benefit this.
Another key consideration is the economic benefits that Industry 4.0 will bring. While previously the systems and machines across the sector were centrally controlled, as a result of current developments machines will start to act more independently as well as communicate directly without reference to a central system or human beings. Products will be able to communicate to a machine how they should be produced and even calculate how to save money during the production process.
However, as with all aspects of life not everyone will come out on top. Some businesses will win – as will some individuals – but others will lose. The financial struggles of recent years have demonstrated that no company is truly indestructible. Changing times and technologies have impacted banks, newspapers and high street stores. If food manufacturers want to avoid similar fates then they must be prepared for the future.
This means, first and foremost, accepting that change is upon us. Companies must keep abreast of the changes that are already taking place, as well as those that may take place in the future. They must listen to experts, embrace new technology, big data and other new developments – not just for their own good, but that of the industry at large.
This sort of progress won’t take place overnight. It will be years before it is fully realised, but many of the building blocks are already in place. The journey has already begun.