Quality assurance: the greatest business strategy
- Like
- Digg
- Del
- Tumblr
- VKontakte
- Buffer
- Love This
- Odnoklassniki
- Meneame
- Blogger
- Amazon
- Yahoo Mail
- Gmail
- AOL
- Newsvine
- HackerNews
- Evernote
- MySpace
- Mail.ru
- Viadeo
- Line
- Comments
- Yummly
- SMS
- Viber
- Telegram
- Subscribe
- Skype
- Facebook Messenger
- Kakao
- LiveJournal
- Yammer
- Edgar
- Fintel
- Mix
- Instapaper
- Copy Link
Posted: 20 August 2020 | Gizem Kayar | 4 comments
Quality expert Gizem Kayar explains the role of a Quality Assurance manager and the challenges industry face.
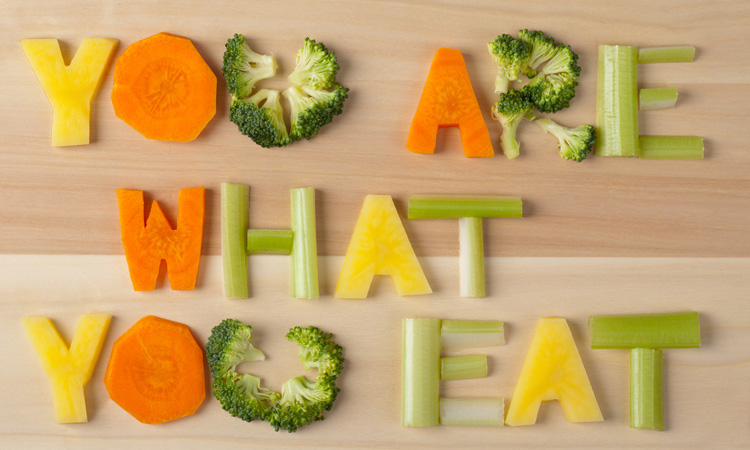
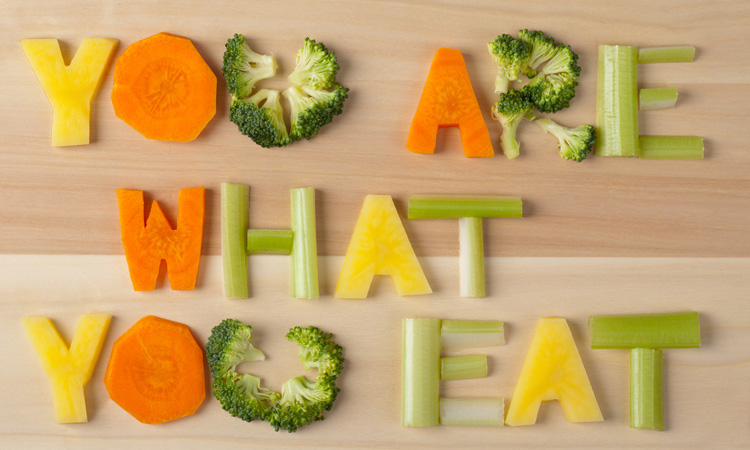
Quality comprises many elements and is difficult to define. In the most basic terms, it describes the value and satisfactory state of a product, but it is a complex concept that includes many facets, most of which are subjective.
Quality considerations
When it comes to quality one must consider the following:
- Product characteristics and performance
- Customer expectations
- Value for money.
Product characteristics and performance, such as physical, chemical and microbiological profiles of the product, as well as compliance to the product specification, are measurable features. Whereas, customer expectations of smell, taste, colour, texture and other eating characteristics of a product vary infinitely, and meeting these can be quite challenging.
The role of Quality Assurance
The main role of a Quality Assurance (QA) department is to ensure all these quality aspects meet with the necessary requirements (eg, legal, customer, internal/external standards), along with continuous maintenance and improvement of quality, record keeping, reporting, problem hunting and solving, and, ultimately, making sure a safe, high quality product is delivered to the customer.
QA, which cannot be thought of as a separate term from safety, includes different steps and comprehensive control mechanisms. First, establishing a plan according to a QA management system is crucial. This plan is unique for each manufacturer, so it must be tailored proficiently. It should include not only inspections, testing and monitoring activities as the part of quality control, but also additional activities to prevent food safety hazards and quality defects.
Responsibilities of the QA manager vary business to business and will depend on the scale of the company
The most common tool used in food manufacturing is the HACCP system. This gives QA managers a chance to recognise their processes step-by-step, identify the critical points, prevent the potential hazards before occurrence, and/or when things go wrong, identify the action points. Although the focus of the HACCP system is food safety, it is also fundamental for product quality.
QA is the backbone of food manufacturing; food has a direct effect on health and can be lethal if proper protocol is not followed. I strongly believe that ‘you are what you eat’. Maintaining quality means you can be confident that you are delivering safe and consistent products that meet consumer demands.Some of the main steps a QA food manufacturing site must take include regular GMP audits to monitor site standards, microbiology testing of materials and inspection of finished products via sampling. Also, a thorough sanitation process, with swabs taken to indicate cleanliness and hygiene, and daily taste panels based on sensory analysis.
Building consumer trust through consistency is key, it not only keeps you ahead of the competition, but also helps to create a loyal relationship between you and the customer.
A successful QA system should let companies sell products with few worries, minimise economic loss and enhance safety. With appropriate QA, a business should have clear traceability, empowering it to detect and, in some cases, prevent an incident before it occurs.
Quality Assurance managers
Responsibilities of the QA manager vary business to business and will depend on the scale of the company. In bigger organisations, a QA manager generally focuses on writing guidance to assure quality and make sure quality control tasks are being followed by the team.
The main role of a Quality Assurance (QA) department is to ensure all these quality aspects meet with the necessary requirements
Whereas in SMEs, a QA manager’s role could comprise hygiene, pest control, quality control, food safety and defence, raw material/packaging supplier quality and documentation, regulatory compliance and responding to customer complaints, among other responsibilities that are assigned to them.
Challenges
The challenges of QA will vary depending on the business, but I personally believe the two biggest obstacles are continuous human error and lack of commitment to the applications of QA.
Human error and commitment
Automated companies have the advantage of more rigid processes and control mechanisms, meaning there is less chance of human error. Unfortunately, automation is not an option for a lot of SMEs, due to restrictions such as space and cost, and therefore, human error is inevitable.
Minimal investment in quality tools, resistance to change, and lack of commitment by departments to QA applications can be very challenging.
We cannot underestimate the future effects of this pandemic on QA
Commitment to quality and safety from senior management is the first requirement of the BRC standards. It is also important that these teams remain open-minded about system changes, as these can enhance both safety and quality. The senior team needs to have a clear plan for maintenance and improvement of food safety and quality culture, provide the required human and financial resources, and ensure they are involved in meetings on a regular basis. If not fulfilled, the success of the quality and safety systems can never reach the high level of confidence that consumers expect and require.
Consumer driven
Recently, globalisation and fast-changing customer behaviours have led to an array of choice. As a result, there is now stronger competition in the food sector. Today, customers choose their food according to trends (eg sustainability, vegan, healthy options, etc.), they are more aware about the nutritional contents, and they have specific dietary preferences and needs. There has been a clear power shift, with savvy shoppers dominating industry decisions.
Businesses have had to become more personalised and ‘reliable’ to survive, in other words be more attuned with shoppers’ wants and needs. It has now become common for industry to work closely with their customers and, consequently, give much more attention to quality and safety procedures than before.
Regulation
It is worth noting that the number of regulations and governmental/third-party audits have recently increased, which, in turn, has increased concern among manufacturers to ensure systems comply. There is also easier access to international quality standards that specify the requirements for implementation and maintenance of quality systems. This means businesses can initiate change more quickly in order to meet a new set of regulations.
COVID-19
I must mention the very big challenge facing all of us, namely COVID-19. We cannot underestimate the future effects of this pandemic on QA.
Many food manufactures have already taken precautions so to maintain food safety and quality, and the well-being of their staff. Such measures include temperature checks of every individual before they enter the factory, restricted access to sites, social distancing, stricter rules for PPE use (including additional PPE), and virtual audits. These are but a few examples of the ‘new normal’ and I do not doubt there will be even bigger changes in QA and safety to come.
About the author
Gizem Kayar is Quality Assurance Manager at Graze, a UK health foods company, which began its journey with the delivery of snack parcels through letterboxes, and since has developed several supermarket partnerships. Gizem has extensive expertise in quality management systems, HACCP, governmental audits and legal compliance, as well as research experience in food technology. She is qualified in Food Engineering (BEng) and Food Science and Nutrition (MSc).
Very well written article Gizem. It highlights the importance of QA from business perspective. The image used is very catchy for the common reader too.
Hello,
Really nice article and very informative. Thanks for sharing
Hi Gizem,
Very comprehensive article explaining why Quality Assurance is the greatest business strategy, Gizem. Your detailing on the challenges faced by Quality Assurance especially in the food sector is worth a mention. I completely agree to the fact that it has now become common for industry to work closely with their customers and, consequently, give much more attention to quality and safety procedures than before.
Content is worthy and informative. Thanks for the information.