Methods to evaulate packaging performance
- Like
- Digg
- Del
- Tumblr
- VKontakte
- Buffer
- Love This
- Odnoklassniki
- Meneame
- Blogger
- Amazon
- Yahoo Mail
- Gmail
- AOL
- Newsvine
- HackerNews
- Evernote
- MySpace
- Mail.ru
- Viadeo
- Line
- Comments
- Yummly
- SMS
- Viber
- Telegram
- Subscribe
- Skype
- Facebook Messenger
- Kakao
- LiveJournal
- Yammer
- Edgar
- Fintel
- Mix
- Instapaper
- Copy Link
Posted: 13 May 2011 | Emma Hanby, Innovation Advisor, Campden BRI | No comments yet
Food packaging is core to managing the delivery of innovative, safe products to the consumer. The consumer has an increasing awareness of the impact of packaging on the environment. With the advent of the Courtauld Commitment to reduce the amount of packaging materials being sent to landfill, an increasing number of companies are exploring routes to lightweight material or are using alternative materials. The Courtauld Commitment is a voluntary agreement between major UK supermarkets and the Waste and Resources Action programme (WRAP). It aims to reduce household waste by achieving reductions in packaging waste growth and identify solutions to reduce food waste.
In 2010, we saw Asda trial reusable packaging for fabric conditioner, Sainsbury’s move from cans to combibloc cartons for its Basics range of canned tomatoes, Nestle remove plastic inserts from Easter Egg packaging, Stella Artois launch a lightweight glass bottle and Waitrose use flow wrap packs for minced beef. We also saw the move to wine in pouches and PET bottles, cereal without cartons and milk in bags.
Food packaging is core to managing the delivery of innovative, safe products to the consumer. The consumer has an increasing awareness of the impact of packaging on the environment. With the advent of the Courtauld Commitment to reduce the amount of packaging materials being sent to landfill, an increasing number of companies are exploring routes to lightweight material or are using alternative materials. The Courtauld Commitment is a voluntary agreement between major UK supermarkets and the Waste and Resources Action programme (WRAP). It aims to reduce household waste by achieving reductions in packaging waste growth and identify solutions to reduce food waste. In 2010, we saw Asda trial reusable packaging for fabric conditioner, Sainsbury’s move from cans to combibloc cartons for its Basics range of canned tomatoes, Nestle remove plastic inserts from Easter Egg packaging, Stella Artois launch a lightweight glass bottle and Waitrose use flow wrap packs for minced beef. We also saw the move to wine in pouches and PET bottles, cereal without cartons and milk in bags.
Food packaging is core to managing the delivery of innovative, safe products to the consumer. The consumer has an increasing awareness of the impact of packaging on the environment. With the advent of the Courtauld Commitment to reduce the amount of packaging materials being sent to landfill, an increasing number of companies are exploring routes to lightweight material or are using alternative materials. The Courtauld Commitment is a voluntary agreement between major UK supermarkets and the Waste and Resources Action programme (WRAP). It aims to reduce household waste by achieving reductions in packaging waste growth and identify solutions to reduce food waste.
In 2010, we saw Asda trial reusable packaging for fabric conditioner, Sainsbury’s move from cans to combibloc cartons for its Basics range of canned tomatoes, Nestle remove plastic inserts from Easter Egg packaging, Stella Artois launch a lightweight glass bottle and Waitrose use flow wrap packs for minced beef. We also saw the move to wine in pouches and PET bottles, cereal without cartons and milk in bags.
Choosing the correct packaging is key to ensuring safe delivery of product through the supply chain. By evaluating the performance of materials used for packaging, specifications can be drawn up to aid the reduction in the amount of packaging being used without compromising product safety.
Alongside the move to reduce the amount of packaging ending up in landfill, companies and government bodies also aim to reduce the amount of food waste going to landfill. It is likely that there is a strong link between the role of packaging and food waste.
The function of packaging
The need for packaging is sometimes questioned. However, packaging can prevent microbiological growth, product deterioration and chemical contamination, it can protect food from light and moisture and it can protect from physical damage. It is also vital for carrying legally required and other information about the food. In essence, packaging carries out three functions: protection, preservation and promotion of the product. The first two of these functions directly impact on food waste as they reduce the rate of deterioration.
The three functions described are achieved by primary, secondary or tertiary packaging alone or in combination. Primary is the term applied to packaging in direct contact with the food. Secondary packaging houses a number of primary packs, for example, the cardboard sleeve of a multipack of drinks cans or the outer plastic wrapper of a multipack of crisps. Tertiary packaging refers to the transport container which is a pack made up of a number of secondary packs. In order for us to understand how packaging performs these three functions, it is important to understand why certain materials are used. The key materials are plastic, metal, glass and board.
Plastics
Plastics are typically polymers of high molecular mass. They are very adaptable, having both technological and aesthetic properties that make them ideal for food use:
- Can be moulded, shaped and deformed
- Rigid or flexible
- Generally lightweight
- Provide barriers to light, moisture and certain gases when required
- If the application requires it, can be heat sealed together
- Can be coloured
- A high quality print can be achieved on smooth surfaces
Metal
Metal food packaging is generally manufactured from steel or aluminium. Steel cans are generally used for food and beverages, whereas aluminium is typically used for beverages. Metal can also be used as a laminate in pouch applications and in its simplest form for cheese, chewing gum and stock cubes. Metal packaging is chosen for a number of reasons:
- Relatively high strength and stiffness
- Good formability
- Good impact resistance
- Good thermal conductivity
Glass
Glass is the oldest packaging material known to man. It can be produced in a variety of shapes and sizes. It is chemically inert and provides long term containment for a number of food stuffs. It is suitable for hot filling, thermal processing and chilled storage. Other characteristics include:
- Consumer appeal, glass can be perceived as packaging for quality/luxury items
- It is impermeable to all gases and moisture
Board
Paper and paper board are primarily cellulose fibres derived from wood. They can be used as a primary packaging container but more typically are used as a transport container, in corrugated form. The characteristics making them suitable for food packaging include:
- Good light barrier
- Light weight
- Provide a good surface for printing
- Provide rigidity for delicate products
Packaging as a protector
During product development, the packaging will be chosen for its ability to protect, preserve and promote. Promotion is typically through colour, shape and branding. Preservation can be tested through shelf-life trials and on evaluation of the suitability of the packaging to the food.
However, when considering how the packaging will aid protection, the movement of the product through the distribution chain must be taken into account. A recent survey carried out by Campden BRI found that 78 per cent of companies surveyed have recorded packaging damage in the supply chain in the past 12 months.
There are a number of tests that are employed by packaging manufacturers during design and manufacture of packaging to test its ‘fitness for purpose’. These tests can also be used by food manufacturers and independent test houses as investigatory tools as part of research into packaging performance. One of the tests commonly used in the packaging industry is compression testing.
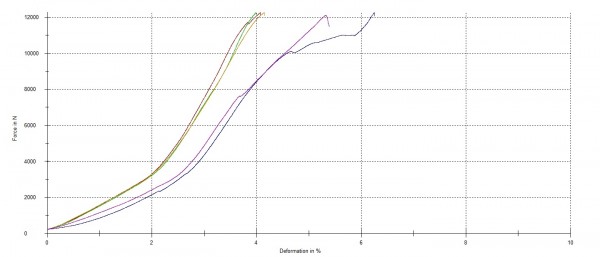
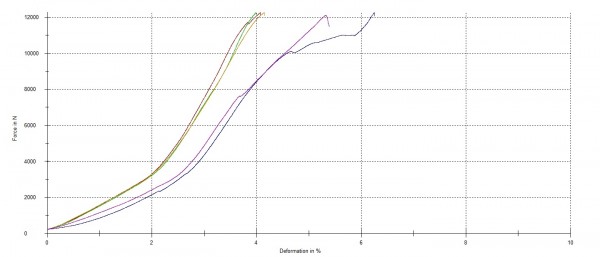
Figure 1 Graph to show force in Newtons plotted against % deformation
This determines the behaviour of materials under crushing loads. This test can be used to calculate the performance of a distribution package with respect to compressive forces and so its ability to protect its contents during compression. It can also be used to measure stacking strength. This is particularly important in storage and distribution where space is at a premium. This ensures the packs can withstand the compressive force exerted upon them when stacked. An external load is applied to the container to replicate the load applied when containers are stacked. By using the correct grade of carton board, the packaging will protect its contents during storage and distribution without being overıspecified and therefore unnecessarily expensive.
A recent study at Campden BRI was commissioned by a large food company to test the ‘fitness for purpose’ of corrugated cartons in protecting their contents during storage and distribution without using excessive packaging. The specification for the cartons required that a compression load of 12250N would result in less than 20 per cent dimensional deformation.
Ten cartons were tested using BS EN 22872:1993. Complete, filled transport packages –method for determination of resistance to compression. Cartons were pre-conditioned at 23°C/ 50 per cent relative humidity (RH) for >16 hours prior to testing. Maximum force applied was 12250N, the compression tester automatically ended the test if the carton deformed by more than 20 per cent.
Table 1
Sample Number | Fmax (N) | dL at Fmax (mm) | F at break (N) | dL at break (mm) |
1 | 12251.25 | 10.9 | – | – |
2 | 12250.81 | 10.6 | – | – |
3 | 12249.22 | 16.7 | – | – |
4 | 12251.50 | 11.1 | – | – |
5 | 12102.50 | 14.2 | 11500 | 14.4 |
Table 1 shows that sample five failed at 11500N and so we concluded that 80 per cent of the containers comply with the company’s requirements. Typically, during a compression test the following characteristics are seen:
- Buckling: this is characterised by sudden failure caused by compressive force
- Shearing (or shear force): characterised by a sliding failure. The shear strength of a material can help to determine the dimensions of a package
The resistance to the compressive force applied to a board container is related to a number of factors. Strength properties increase with thickness but can be reduced by an increase in moisture content. All paper and board products will seek to achieve moisture content in equilibrium with ambient conditions. This is known as hygrosensitivity. With corrugated containers, the board type and flute type will also influence the strength properties. Corrugated board samples range from single face (comprised of one liner and one flute layer) to triple wall (made up of four liners and three flute layers) with strength increasing respectively. Figure 2 shows a single walled board sample.
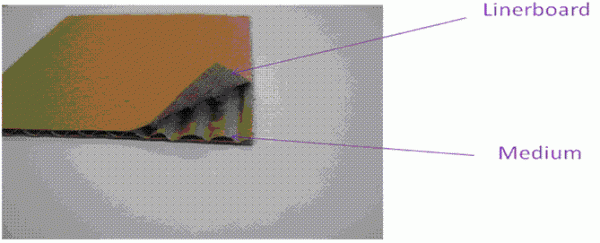
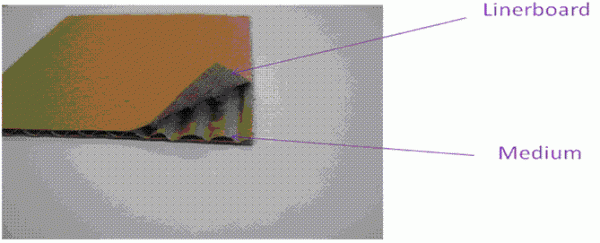
Figure 2 Single walled board sample
Flutes provide rigidity and can make the board more economical. The flute profile will affect strength; higher flutes (B flutes) provide a physically stronger stack with softer cushioning characteristics. Lower, more dense flutes (E flutes) provide greater flat crush resistance, smoother print surfaces and crisper score lines. The most common flute type used in the UK is ‘B’. Figure 3 shows some of the different flute types in use.
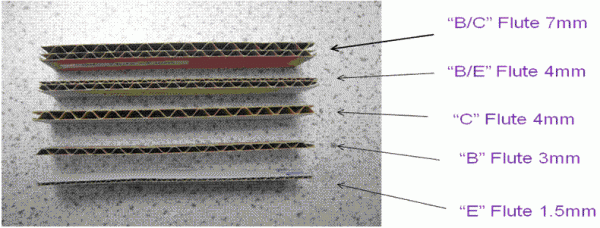
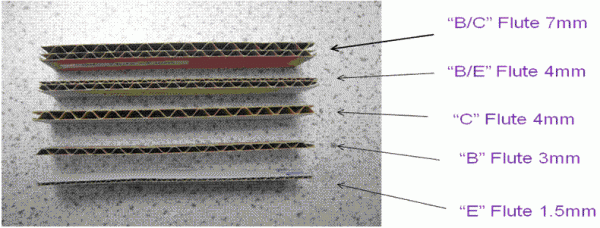
Figure 3 Flute types
B flute is used for canned food as it has good end-to-end compression attributes. C flute is used for more delicate products, as it has a good stacking strength. E flute is commonly used for point of purchase display containers as it provides a good surface for printing graphics.
More and more companies are looking to include higher proportions of recycled content in their packaging, but this too can affect strength. Flute manufactured from recycled board is used for general performance but when more strength is required or the packaging is to be stored in humid conditions, it is recommended to use virgin material. It is understood that products manufactured from recycled board tend to have an unpredictable structure and inferior functional properties to virgin based boards. The compression test described above is not restricted to board and corrugated board; it can also be useful to measure the resistance of metals, glass, plastic and composite containers to compression forces.
An emerging example is in the drinks industry. The industry is trialling the use of lighter weight glass for wine and other brewed drinks. Compression testing can be used to evaluate the vertical load capacity of such containers. Glass containers are required to withstand compressive forces to ensure they do not break. This type of test replicates the types of forces applied during capping and stacking.
Conclusion
In conclusion, packaging is essential as it serves three functions; it protects, preserves and promotes. The food and packaging industries have been optimising packaging for some years to reduce cost and environmental impact and will continue to do so. There is a strong link between the protection of packaging and the reduction in food waste. Methods must be employed by the food and packaging industries to evaluate the performance of packaging. It is a key tool to preventing food waste.
Compression testing can be a useful tool to measure the performance of packaging. It ensures that products are protected without the packaging being over-specified and therefore unnecessarily expensive. There is hard evidence that performance is linked to the strength properties of a material. In the case of board packaging, strength is increased with thickness, flute type and the origin of the material. Compression testing can help food and packaging manufacturers select the best packaging for the job. This test can also be used to evaluate the performance of metals, glass, plastic and composite containers.
Further information
- Hutton,T. (2003) Food packaging: an introduction. Key topic in Food Science and Technology No. 7. Campden BRI.
- Videos on packaging testing – www.campden.co.uk/videos.htm
About the Author
Emma Hanby is an Innovation Advisor at Campden BRI. A graduate in Food Science and Nutrition, Emma worked in industry, including spells at Northern Foods and Waitrose, before joining Campden BRI (then Campden and Chorleywood Food Research Association) in 2004. Her role includes undertaking packaging research and providing consultancy to the food and drink manufacturing industry. Emma has co-authored and published a number of research articles and other publications and presented at conferences and other events internationally on food packaging related issues.