The growth of the bio-lubricant industry
- Like
- Digg
- Del
- Tumblr
- VKontakte
- Buffer
- Love This
- Odnoklassniki
- Meneame
- Blogger
- Amazon
- Yahoo Mail
- Gmail
- AOL
- Newsvine
- HackerNews
- Evernote
- MySpace
- Mail.ru
- Viadeo
- Line
- Comments
- Yummly
- SMS
- Viber
- Telegram
- Subscribe
- Skype
- Facebook Messenger
- Kakao
- LiveJournal
- Yammer
- Edgar
- Fintel
- Mix
- Instapaper
- Copy Link
Posted: 10 December 2019 | Dionisios G. Vlachos, Sibao Liu, Sunitha Sadula | No comments yet
Sibao Liu, Sunitha Sadula and Dionisios G. Vlachos, academics from the University of Delaware, discuss how safety, environmental and sustainability concerns have driven the growth of the bio-lubricant industry, and how innovative approaches have looked to overcome these challenges.


Food grade lubricants contribute to a safer food supply and bio-based food grade lubricants contribute to a safer and sustainable future for the planet. Food-grade lubricants in machinery serve the same purpose as other lubricants in many applications. However, the direct consumer-use of products such as food, beverage, medicine and supplements, cosmetics, animal feed and pet food requires more stringent safety and purity specifications.1-5 The global market size of food grade lubricants is projected to reach 64.5 kilotons by 2021, registering a CAGR of 6.7 percent from 2016. In terms of value, the market size for food grade lubricants is projected to grow at a CAGR of seven percent from US $182.8 million in 2016 to $256.5 mn by 2021.6 The rapid growth of the healthcare industry, the increased demand for processed food, and the growth of auxiliary industries, such as packaging, have led to the growth of the food grade lubricants market.
In terms of value, the market size for food grade lubricants is projected to grow at a CAGR of seven percent from US $182.8 million in 2016 to $256.5 mn by 2021
Food-grade designations
The US Department of Agriculture (USDA) created the food-grade designations H1, H2 and H3 based on the way they contact food.1-3 H1 category lubricants are acceptable in food-processing environments where there is a possibility of incidental food contact with a limit of 10 ppm. Three types of base oils are used in these formulations and they are high purity white mineral oils, synthetic base oils such as PAOs (polyalphaolephins), PAGs (polyalkalene glycols), and vegetable oils. H1 lubricants are specially formulated to be low-hazard, odourless, and tasteless to minimise risks associated with incidental contact of lubricants with food during process operations. The H2 lubricants are used on equipment and machine parts in locations where there is no possibility of contact with food. Most substances generally used for industrial lubricants would be acceptable but should not contain heavy metals such as antimony, arsenic, cadmium, lead, mercury or selenium, and the ingredients must not include substances that are carcinogens, mutagens, teratogens or mineral acids. H3 lubricants, also known as soluble or edible oil, are used to clean and prevent rust on hooks, trolleys and similar equipment.
A large fraction of a lubricant is the base oil. Additives are commonly used on top of the base oil to meet lubricant specifications, such as viscosity, viscosity index, pour point and oxidative stability. Petroleum based lubricants are the leading type of base oils used in this industry and these are poorly degradable and represent an environmental hazard when released.7-9 Specifically, mineral-based lubricants produce oil mist that introduces volatile organic compounds (VOCs) into the air and can cause dermatitis, skin and respiratory track irritation7, 10. The consequences of spilling on the food during processing are serious.11 In addition to the environmental footprint, decreasing petroleum resources have prompted governments and individuals to seek renewable products as replacements for petroleum products.
Bio-lubricants
These safety, environmental, and sustainability concerns drive growth of the bio-lubricant industry. Bio-lubricants may be defined generally as materials that are based on biodegradable and renewable-based feedstocks. However, this definition is not universally accepted. In some areas, only biodegradability is considered. As determined by the Secretary of Agriculture, bio-based products are commercial or industrial products (other than food) derived wholly or in significant part of bio-based feedstocks including renewable agricultural materials (plant, animal, and marine materials) or forestry materials.12 Vegetable oil-based lubricants, known for a long time, are renewable and mostly biodegradable, and thus can be considered as a promising substitute to conventional lubricant.13, 14 However, low oxidative, thermal and hydrolytic stability, poor low-temperature properties and narrow range of available viscosities limit their direct use as base oils. These limitations can be mitigated by proper chemical modification, formulation with additives, and blending with mineral oils; however, these result in increasing cost, toxicity and decrease in biodegradability. Thus, developing a cost-effective bio-based lubricant with revolutionary combination of biodegradability and high lubricant properties is a big challenge.
Bio-lubricants may be defined generally as materials that are based on biodegradable and renewable-based feedstocks
Recent innovative and strategic approaches show that lignocellulose has the potential to address this challenge and narrow down the gap between vegetable and petroleum based lubricants. In this context, a California based US company, Novvi LLC, developed the first sugar cane derived 100 percent renewable base oil which is certified by NSF (National Sanitation Foundation) as an H1 grade high performance food-based lubricant.15 Bell and co-workers reported the self-condensation of vegetable oil and lignocellulose derived ketones and hydrogenation/hydrodeoxygenation (HDO) of the condensation products to produce cycloalkane base oils.16-18
These cycloalkane base oils have shown excellent pour points and 80 percent reduction in greenhouse gas emissions but have some property compatibility issues, in viscosity and viscosity index (VI) for example, when compared with commercial synthetic base oils. CCEI (the Catalysis Center for Energy Innovation) at the University of Delaware developed an entire suite of chemistries for the production of renewable lubricant base oils with tunable properties using vegetable oil and lignocellulose derived based feedstocks.19-21 A main advantage of this portfolio of technologies is the specificity in degree of branching, molecular weight, and functional group in these molecules. Their properties are as good as, or often better, than commercially available high-performance lubricants. The cost of fatty acids co-processed with furans, derived from cellulose and hemi-cellulose, is currently a limitation, but use of recycled/waste oils and fat mitigates this problem. The biodegradability of these new products needs to be tested.
The bio-lubricant area will grow faster in the next years across industries and transportation
Recognised as potential substitutes to petroleum-based lubricants and promoted by government regulations, such as federal government BioPreferred programme12, the bio-lubricant area will grow faster in the next years across industries and transportation. Moving towards business sustainability, companies would have to create economic values by contributing to a sustainable and healthy environment, without compromising and affecting future generations. Hence, use of low toxicity bio-lubricants would probably be enforced in environmentally sensitised areas and in the food industry. Significant research efforts are needed to develop economical and high performing bio-based lubricants with excellent biodegradability that will one day replace mineral oil-based or PAOs-based lubricants in various industries.
About the authors
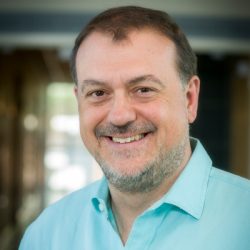
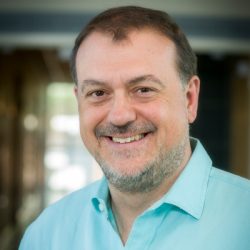
Dionisios G. Vlachos
Dionisios G. Vlachos is the Allan and Myra Ferguson Professor of Chemical & Biomolecular Engineering, a Professor of Physics and Astronomy at the University of Delaware (UD); Director of the University of Delaware Energy Institute (UDEI) and the Catalysis Center for Energy Innovation (CCEI), an Energy Frontier Research Center (EFRC); and Focus Area Leader of the manufacturing institute RAPID at UD. He is the ExxonMobil Visiting Chair Professor, National University of Singapore, Singapore, 2018-2021.
Dr. Vlachos’ main research thrusts entail circular economy and waste derivatisation, multiscale modelling and simulation, distributed (bio)chemical manufacturing, process intensification and novel catalytic reactors, renewable fuels and chemicals, catalyst informatics and in silico materials prediction, and kinetic modelling of biomass, shale gas, nitrogen cycle, and CO2 cycle.
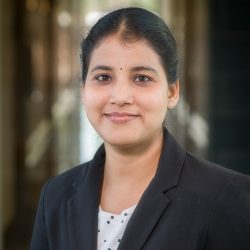
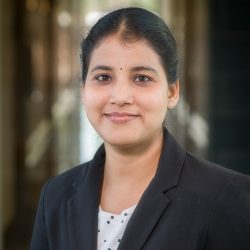
Sunitha Sadula
Sunitha Sadula is a Senior Research Associate at the University of Delaware’s Catalysis Center for Energy Innovation (CCEI), an Energy Frontier Research Center. She received her MS in Industrial Chemistry from the National Institute of Technology, Warangal and PhD in Chemistry from the Indian Institute of Chemical Technology, Hyderabad, India. Dr. Sadula spent two years conducting postdoctoral research at Iowa State University, then worked for a year at Indian Oil Corporation Limited as a Scientific Officer. In 2015, she came to the University of Delaware to continue her postdoctoral research for three years before becoming a Senior Research Associate.
Dr. Sadula’s research focuses on catalytic process development for the conversion of bio-renewable feedstocks to fuels and chemicals. She has published over twenty papers, one patent and received more than 500 citations.
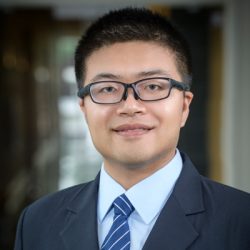
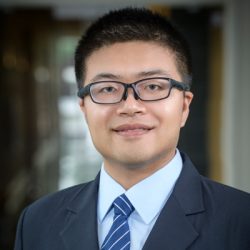
Sibao Liu
Sibao Liu is a Senior Research Associate at the University of Delaware’s Catalysis Center for Energy Innovation (CCEI), an Energy Frontier Research Center. He received his BS and MS in Chemical Engineering from Dalian University of Technology and his PhD in Applied Chemistry from Tohoku University. Prior to joining the University of Delaware as a postdoctoral researcher, he held the same position for four months at Tohoku University.
Dr. Liu focuses his research on the development of novel heterogeneous catalysts and processes for the conversion of biomass and solid organic wastes to fuels and valuable chemicals. He has more than 20 publications and over 800 citations.
References
- Gebarin, S., The Basics of Food-grade Lubricants. Machinery Lubrication 2009, 131.
- Sniderman, D., Food grade lubricants and their regulation. Tribology & Lubrication Technology 2016, 72 (1), 26.
- Williamson, M., Understanding food-grade lubricants. Machinery Lubrication Magazine 2003, 64.
- Moens, E., Production and use of food-grade lubricants. Trends in Food Science & Technology 2003, 14 (4), 157-162.
- Małysa, A., The safety and functionality of food grade lubricants. Current Trends in Commodity Science Challenges in Food Development and Processing, Editors Urszula Samotyja, Wojciech Zmudziński, Poznań 2017, 177-192.
- https://www.prnewswire.com/news-releases/…
- Moon, M., How clean are your lubricants? Trends in food science & technology 2007, 18, S74-S79.
- Mang, T.; Dresel, W.; Wiley, J., Lubricants and lubrication. Wiley-Vch Weinheim, Germany: 2007; Vol. 2.
- Schneider, M. P., Plant‐oil‐based lubricants and hydraulic fluids. Journal of the Science of Food and Agriculture 2006, 86 (12), 1769-1780.
- Girard, J.; Officer, C. M., The continuing evolution of food grade lubricants. Machinery Lubrication Magazine 2002, 20.
- https://www.foodengineeringmag.com/…
- https://www.dm.usda.gov/procurement/…
- Syahir, A.; Zulkifli, N.; Masjuki, H.; Kalam, M.; Alabdulkarem, A.; Gulzar, M.; Khuong, L.; Harith, M., A review on bio-based lubricants and their applications. Journal of Cleaner Production 2017, 168, 997-1016.
- Emmanuel O. Aluyor, K. O. O. a. M. O.-j., Biodegradation of vegetable oils: A review. Scientific Research and Essay 2009, 4 (6), 543-548.
- https://novvi.com/novaspec-base-oils/.
- Balakrishnan, M.; Sacia, E. R.; Sreekumar, S.; Gunbas, G.; Gokhale, A. A.; Scown, C. D.; Toste, F. D.; Bell, A. T., Novel pathways for fuels and lubricants from biomass optimized using life-cycle greenhouse gas assessment. Proceedings of the National Academy of Sciences 2015, 112 (25), 7645-7649.
- Balakrishnan, M.; Arab, G. E.; Kunbargi, O. B.; Gokhale, A. A.; Grippo, A. M.; Toste, F. D.; Bell, A. T., Production of renewable lubricants via self-condensation of methyl ketones. Green Chemistry 2016, 18 (12), 3577-3581.
- Shylesh, S.; Gokhale, A. A.; Sun, K.; Grippo, A. M.; Jadhav, D.; Yeh, A.; Ho, C. R.; Bell, A. T., Integrated catalytic sequences for catalytic upgrading of bio-derived carboxylic acids to fuels, lubricants and chemical feedstocks. Sustainable Energy & Fuels 2017, 1 (8), 1805-1809.
- Liu, S.; Josephson, T. R.; Athaley, A.; Chen, Q. P.; Norton, A.; Ierapetritou, M.; Siepmann, J. I.; Saha, B.; Vlachos, D. G., Renewable lubricants with tailored molecular architecture. Science advances 2019, 5 (2), eaav5487.
- Liu, S.; Saha, B.; Vlachos, D. G., Catalytic production of renewable lubricant base oils from bio-based 2-alkylfurans and enals. Green Chemistry 2019, 21 (13), 3606-3614.
- Norton, A. M.; Liu, S.; Saha, B.; Vlachos, D. G., Branched Bio‐Lubricant Base Oil Production through Aldol Condensation. ChemSusChem 2019.
Related topics
Food Grade Lubricants, Food Safety, Regulation & Legislation, Research & development
Related organisations
National Sanitation Foundation (NSF), Novvi LLC, University of Delaware