Better On-The-Job Training with Digital One Point Lessons
- Like
- Digg
- Del
- Tumblr
- VKontakte
- Buffer
- Love This
- Odnoklassniki
- Meneame
- Blogger
- Amazon
- Yahoo Mail
- Gmail
- AOL
- Newsvine
- HackerNews
- Evernote
- MySpace
- Mail.ru
- Viadeo
- Line
- Comments
- Yummly
- SMS
- Viber
- Telegram
- Subscribe
- Skype
- Facebook Messenger
- Kakao
- LiveJournal
- Yammer
- Edgar
- Fintel
- Mix
- Instapaper
- Copy Link
Posted: 24 April 2020 | SwipeGuide | No comments yet
Improve procedures and standards with digital One Point Lessons on the shop floor. Eliminate paper training tools and gain the edge in Industry 4.0.
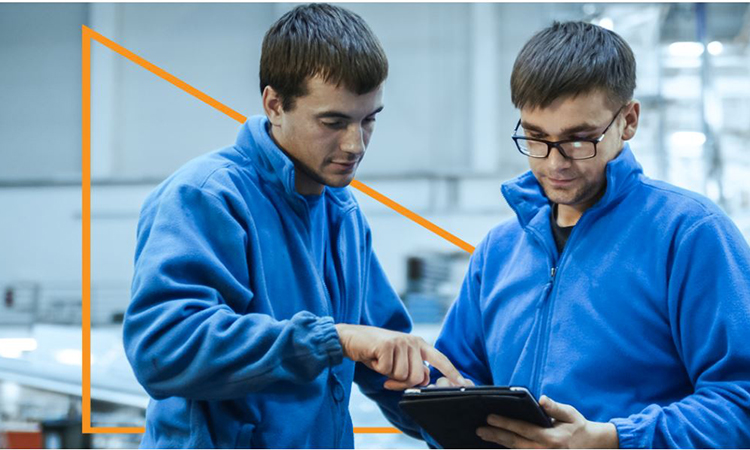
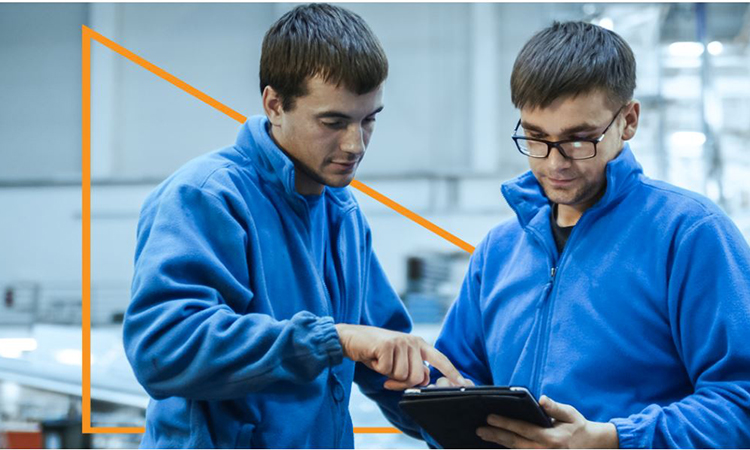
Digital One Point Lessons [OPLs] allow you to deliver knowledge more efficiently to your deskless workforce and improve processes while creating a better digital learning experience.
What is an OPL?
OPLs are simple training tools designed to reinforce and clarify Standard Operating Procedures [SOPs] on the shop floor. These simple, highly visual lessons are used to reinforce key skills for deskless workers and address particular problems and bottlenecks in production.
In the past, One Point Lessons have been visualized on paper and distributed or displayed from a centralized location such as a whiteboard or a Team Corner. However, as our factories become more complex and the skill-set of our deskless workforce continues to evolve, our training solutions need to scale as well.
Digital work instruction platforms are an excellent way to bring OPLs into modern manufacturing.
Why do we need OPLs?
Sometimes, a process on the shop floor needs to be taught in detail or reinforced. Manufacturers use OPLs to strategically deliver knowledge about processes that may present a particular challenge for teams working on a production line.
We already know that digital work instructions increase productivity and decrease waste by standardizing work and delivering up-to-date knowledge to teams on the shop floor.
Digital work instruction platforms are a natural choice to digitize and distribute existing paper OPLs.
Who creates OPLs?
OPLs are created by subject matter experts who have significant experience with the SOP in question. However, the review and revision process should always be democratic.
What does a great OPL look like?
– Simple.
OPLs should be designed according to the same principles as effective work instructions. This means that they should cover the smallest portion of work possible, and should be limited to one lesson per step.
– Visual.
Humans are visual learners, and One Point Lessons on the shop floor are no exception. The best digital work instruction platforms are highly visual and minimalistic by design. This means that they’re ideal for presenting the detailed and action oriented images (and just the right amount of text) to teach your teams effectively on mobile devices.
– Accessible and centrally located.
By design, OPLs need to be visible and centrally located. Physical OPLs require teams to take the time to move to this location and examine the lesson before returning to their work.
The same technology that delivers knowledge in the moment of need to teams on the shop floor can be used to deliver digital OPLs. Any team, anywhere, can access these valuable insights in the same way that they use digital work instructions.
Example:
Check out the example below from a beverage manufacturing company. Previously, they used a One Point Lesson to reinforce the skills and steps needed to successfully complete a task using a packaging machine.
You can see that each individual step of the task is clearly defined. Headlines are kept simple and scannable to limit confusion and allow teams to learn at their own pace.
Each step of the SOP is displayed in a highly visual manner with limited text. Digital work instruction platforms also allow you to include simple gifs in your OPLs.
Standardize OPLs for global success.
Digital work instruction software allows manufacturers to standardize content by easily sharing work instructions and SOPs throughout their value chains. Make sure that the same effective standards can be efficiently implemented at multiple locations locally and around the world.
Review OPLs for Continuous Improvement.
The principles of Lean philosophy and continuous improvement apply to OPLs too! Make sure that each lesson is reviewed by a new set of eyes, and that feedback is delivered and implemented before they reach the shop floor.
OPLs and Analytics.
Want to take the guesswork out of finding your pain points and bottlenecks? Want to know exactly where a One Point Lesson would be particularly beneficial? The best digital work instruction platforms allow you to pinpoint problem areas in your manufacturing workflows and work instructions with real time data on User Effort Score and Completion Rates.
Integrate with skills management.
OPLs are a great way to track the skills development and professional progress of the teams on your shop floor. Make these informative lessons an essential part of reskilling and training to ensure that teams are working with the most up-to-date knowledge and skills.
Digital solutions for better standard work.
Combined with Digital Work Instructions, One Point Lessons help teams on the shop floor grow their knowledge base and continually improve the way they perform standard work.
Check out this page to learn what makes better work instructions great, and how they can increase productivity and reduce waste on the shop floor.