Acceptance of innovative automatic equipment in the postharvest and food industry
- Like
- Digg
- Del
- Tumblr
- VKontakte
- Buffer
- Love This
- Odnoklassniki
- Meneame
- Blogger
- Amazon
- Yahoo Mail
- Gmail
- AOL
- Newsvine
- HackerNews
- Evernote
- MySpace
- Mail.ru
- Viadeo
- Line
- Comments
- Yummly
- SMS
- Viber
- Telegram
- Subscribe
- Skype
- Facebook Messenger
- Kakao
- LiveJournal
- Yammer
- Edgar
- Fintel
- Mix
- Instapaper
- Copy Link
Posted: 26 April 2016 | Idoia Olabarrieta, Senior Researcher, Food Research Division, AZTI-Tecnalia / Izaskun Pérez, Senior Researcher, Food Research Division, AZTI-Tecnalia / Raquel Rodríguez, Food Researcher, Food Research Division, AZTI-Tecnalia / Jaime Zufía, Head of the Efficiency and Sustainability Department, AZTI | No comments yet
PICKNPACK1 is a large collaborative project granted by the EU within the 7th Frame programme, with the aim of boosting the development and implementation of innovative automatic systems in food industry. In order to find strategic approaches for facilitating greater deployment of new flexible and autonomous robots, sensors and packaging modules in the food industry of today, an acceptance study was done within this sector. This article summarises the main conclusions achieved from that study for both food processing and postharvest sector.
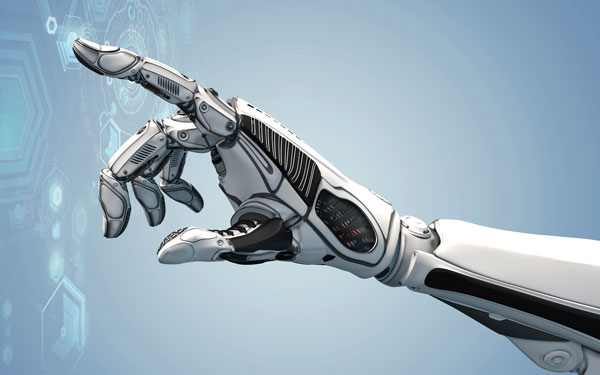
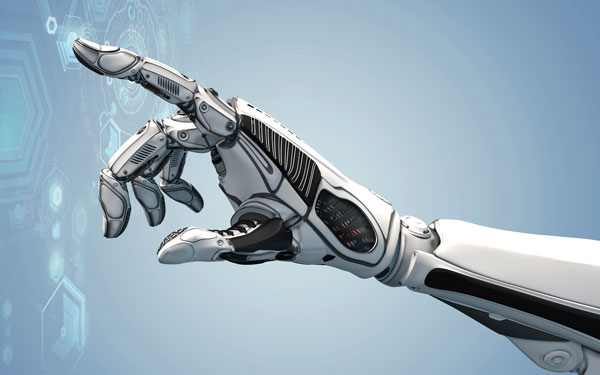
Introduction
Automation and robotics have penetrated in many industrial operations. As production demand increased, larger food companies saw the benefit of automation. At the beginning these new systems were implemented on the high-volume, long-life, single-product lines. Many food industries have automated with great success their palletising and secondary packaging applications2 . However, recent technology advancements, coupled with more challenging production demands, have caused a trend of innovative automatic systems (robots, sensors, etc.) migrating further up in the processing line including sorting, grading and primary packaging of products.
Small or medium-sized (SME) companies have been much slower in incorporating automation. The high variability of the food products, complexity of the food processes and required high investments, limit the use of automation/robots in food industry. In this sense, research is steadily advancing to meet the requirements and challenges of the small food manufactures. Nonetheless, there is still a significant gap between research on innovative automatic systems and its implementation in food manufacturing. In order to achieve signifi – cant deployment of the innovative automation in all the levels, attention should be given to investigating and analysing the factors which affect the infiltration of these technologies into the industrial food processes.
Methodology
A survey was developed with the aim of obtaining the knowledge about the automation level of the European food industry, the problems and requirements in sorting and packaging and about the predisposition to invest in innovative equipment. Finally, a list of different barriers and drivers were prepared for scoring, regarding their importance when investing in new equipment. The survey was made by telephone interviews with 15-20 minute structured questionnaires, and also by email through the online questionnaire. Interviewees ranged from Managing, Quality, R&D Directors and Board Members, Owners (Directors), to Chief Engineers or Operations Managers (technicians) from postharvest plants/companies (hereafter referred to as POSTHARVEST) and food processing industries (hereafter referred to as FOOD) in Spain, France, UK, Germany, Netherlands, Belgium and Italy.
Context of the results
81 telephone-interviews/online-surveys were obtained from the 2,250 telephone calls and 800 emails sent, which means an average rate of success of about 2.5%. In summary, 81.5% of the answered surveys were generated by decision makers of the companies (Director, Board members, etc.). The structure of the companies surveyed is indicated in Table 1.
Regarding sectors, 56% of the answers came from the POSTHARVEST sector (tomatoes, table grapes, cucumbers, lettuce, berries, apples, etc.) and 44% from the FOOD sector (ready meals, meat products, wine, cereals and grains, snacks, etc.). The distribution for each country was variable as shown in Table 1. Regarding size, 63% of the total interviewed companies were SMEs (similar percentages were found in both FOOD and POSTHARVEST sectors). Large companies in the study represented 15% and were mainly FOOD companies, whereas cooperatives (17%) were mainly POSTHARVEST companies. 58% of the companies were composed by less than 50 workers, and 80% by less than 250 workers, which means that most of the companies classified as ‘other’ were also small or medium size.
Concerning the amount of processed products in both sectors, the range of different products processed by a single company was greater in FOOD than in POSTHARVEST sector. 87% of POSTHARVEST companies work with less than 10 products, the majority of which (61%) have five or less different products, and only 2% work with more than 50 products. However, a significant part of FOOD companies (≈ 40%) work with more than 10 products, and half of these produce more than 50 different products.
Automation level of the FOOD and POSTHARVEST industry
In a first step, the automation level in the sorting of different quality attributes was analysed (see Figure 1). In POSTHARVEST, size can be outlined as the most automated parameter (47%). The manual control of the sorting in POSTHARVEST is more usual than in FOOD, with almost all the parameters showing higher percentages. The FOOD industry showed higher percentages of no control for the quality attributes analysed. Product size, external defects and foreign matters are the issues more controlled (either manually or automatically), in different levels, in both sectors. However, the general profile of control vs. no control was different in both sectors.
To the question “which parameters are more interesting for your business to improve?” (from 1-insignificant, to 5-very important) POSTHARVEST companies showed more interest in improving sorting, as they assessed for the 10 quality parameters interest above the threshold (established as the midpoint of the scale, score 3). Specifically, size, external defects and foreign matters happened to show the highest interest on average. The size was the highest automated parameter, while foreign matters and external defects were parameters with the highest manual sorting (81%-86%). For FOOD industry, however, the interest was below the threshold except for foreign matters and size parameters, which happened to be the ones more controlled but with a high percentage of manual sorting (55-56%).
Problematic issues
In general, the main problematic SORTING issues cited by companies were linked to external defects detection (≈ 30% of the answers), and to handling of the products (20%). For FOOD sector the most important problems remarked were linked to the handling of the products (33%, normally related to the manual process), external defects (27%) and speed of the process (20%), as shown in Figure 2. POSTHARVEST companies stressed problems on quality detection, external quality problems related to detection of defects (29% of the answers) and internal quality (23%) mainly affecting to organoleptic aspects. In this sector handling issues were mentioned in third position of importance (13% of the answers).
Open answers were also collected for gathering the problems and needs of companies regarding PACKAGING issues. Problems with the filling of the packaging (i.e. precision, manipulation for filling) were the most important ones for both sectors, reported by around 30% of the companies. Problems with labelling and printing as well as with weight control and accuracy were also remarked by both sectors in more than 10% of the cases. As problems specific for each sector it can be mentioned sealing of packaging (19%) for FOOD and traceability (labelling) (15%) for POSTHARVEST.
Interest for improving the business
When asked “where does the company see the greatest interest for investing on innovative equipment for improving the business?”45% of the POSTHARVEST companies cited sensors for more effective quality assessment and more flexible packaging machines (see figure 3). In FOOD sector the most interesting part for improving was the packaging machines (38%) and the palletising system (35%).
When asking about their source of reliable information about innovations and benefits of automated equipment the surveyed companies pointed out the equipment manufacturers and the commercial fairs, in 67% and 43% of the cases, respectively.
Investment intention
POSTHARVEST sector showed higher investment intention in the next years than FOOD processing industry, 71% of positive intention vs. 50%, respectively. This percentage was similar among the SMEs in each sector. Regarding big companies, 80% in FOOD and 100% in POSTHARVEST sector showed intention for investing. Cooperatives and others confirmed also high levels of positive intention, 60% in FOOD and 72% in POSTHARVEST.
Drivers and barriers versus implementation
In order to understand the drivers and barriers that are present in the decision of the companies when investing or not in new equipment, several economic and technological factors were given for them to ranking from insignificant (1) to very important (5).
In a first view, taking into account the scores, the companies that have an intention to invest clearly see the drivers, and the marks given to them are significantly higher than the ones assigned to the barriers, both for FOOD and POSTHARVEST. Regarding the ones with no intention, regardless of the reasons that they may have, it can be noticed that the difference in the score between drivers and barriers is not significant.
Within the drivers, economics is clearly the key factor leading to the investing intention for both sectors. However, the type of economical driver and the priority or score varies between sectors. To gain more information, the relative frequency of scoring for each driver/barrier has been studied and analysed separately depending on the positive or negative investment intention. Thus, it has been considered the percentage of companies assigning each importance level (score from 1 to 5) to each aspect, as shown in Figure 4.
Opportunities and threats of the industry
A more focused analysis of the opportunities that arise in FOOD and POSTHARVEST sectors, led to considering the aspects that already encourage companies to invest, i.e., the drivers of those answering YES to the question of investment intention. Moreover, in the analysis it was decided to take into consideration the drivers of those companies that have a priori NO intention of investing. This decision was based on the fact that the weight assigned to the drivers by the companies with NO investment was not significantly different from that assigned to the barriers. This could help in finding the strategies to strengthen and promote these drivers and tip the balance in favour of the final investment.
Both sectors consider among the main economical drivers (score 5 assigned by more than 50% of companies) to improve the profit margin of the product (74% POSTHARVEST vs. 58% FOOD) and to improve the production efficiency (52% POSTHARVEST vs. 50% FOOD), see Figure 4. As a remarkable difference between both sectors it has been observed that FOOD sector considers to increase the production volume in second place of importance (58% scored 5 points), while POSTHARVEST sector refers the saving in labour cost (67%) in second place. It is also noteworthy that POSTHARVEST sector mentions the differentiation from competitors (52%) and that it considers very important the availability of public funding (63%) to decide to invest. However, FOOD sector does not underline so much the differentiation from competitors (33%) and it is not so dependent on the availability of public funding (17%) for its decision.
Despite that the NO investment intention was lower in POSTHARVEST than in the FOOD sector, the barriers were more highly scored by the POSTHARVEST sector. The three barriers highlighted as the most important by more than 50% of the companies were: investment cost (89%), maintenance and equipment updating cost (67%) and cost and reliability of the technical service (56%). In FOOD sector the importance of the Investment cost was answered in 55% of the cases and the following barrier concept, even if it did not exceeded 50% of the answers, was the structure and size of the company. This is logical since the 80% of the companies with NO investment intention in FOOD sector were SMEs and only 7% were big companies. None technological barrier was assessed with the maximum importance (data not shown).
Conclusion
The POSTHARVEST sector is more sensitive than the FOOD sector to automation investment in the coming years. This is evidenced by a higher assessment of any potential improvement derived from the purchase of a new automated system, as well as a higher weight assigned to the drivers that encourage a possible investment.
The POSTHARVEST as well as the FOOD sector base their investing intention on economic reasons more than on technical aspects. Both sectors consider among the main economical drivers to improve the profit margin of the product and to Improve the production efficiency. However, some differentiating details in the reasons outlined give insight to the key needs in each sector in which to concentrate efforts when designing automated solutions:
- For POSTHARVEST companies the motivation for investing is related to the improvement of the profit margin of the product by the possibility that a new automated solution allows to reduce labor cost and to differentiate from competitors. This needs the development of accurate systems for a more effective quality assessment. The added value provided by a sensor system that examines accurately the 100% of the produced units should facilitate the differentiation and the reduction in labour costs that the sector desires.
- For FOOD companies, the improvement of profit margin of the product is focused on increasing the productive capacity. Their product is characterised by the use of ingredients of different weight, morphology and consistency that are assembled in a packaging of quite different formats (e.g. ready meals). Rapid and flexible solutions for handling and packing the product responding to changes in product or packaging specifications should solve the critical point of the process of food companies.
FOOD and POST-HARVEST industries are aware of the need and benefits of R&D for improving automation and production lines but the risks associated in implementation generate reluctance to invest. In general, SMEs are more reluctant to automate than cooperatives and large companies. Therefore, the prevailing reasons reported for not investing in automation are associated to the structure, and to the limited production volume and economical capacity of such small and medium companies. In particular, the main barriers for investing are economical. It appears that the major barrier is the perception that the high cost of the purchase and maintenance (repair, updating and technical service) of a new automated system is not going to be translated into economic benefits comparable to the investment made. This forces the machine suppliers to better know the manufacturers business and highlights the need to anticipate these economical factors and to estimate the benefits that an automated solution could bring to a particular company. SMEs are the main type of company in food sector3, it is thus necessary to stress this aspect and be knowledgeable when approaching any SME in order to reach a greater uptake of the technology in this vital European economic sector.
In conclusion, the present study has investigated the factors affecting the acceptance of innovative automatic systems by the FOOD processing and POSTHARVEST industry. It has analysed the investment intention of companies in both sectors and the factors that press them to declare a positive or negative intention. The study has also provided a context to these factors. Thus, the knowledge of the particular and common characteristics of both sectors can orient the approaching strategies for generating effective marketing and dissemination plans, in order to facilitate the uptake of the technology within the sector in the food industry of today.
References
- Picknpack-Flexible robotic systems for automated adaptive packaging of fresh and processed food products. www.picknpack.eu [last accessed, November 24, 2015].
- Davis, S. Robotics and Automation for the Food Industry. Food Safety Magazine, 2014. http://www.foodsafetymagazine.com/magazine-archive1/augustseptember-2014/robotics-and-automation-for-the-food-industry/ [last accessed, December 2, 2015].
- Europe, F.D., Data & TRends of the European Food and Drink Industry 2012: http://www.fooddrinkeurope.eu/uploads/publications_documents/Data__Trends_(interactive).pdf. [last accessed, November 16, 2015].
About the authors
Idoia Olabarrieta is an Industrial Engineer with a PhD in polymer technology (KTH, Sweden) working as a Senior Researcher at the Food Research Division of AZTI-Tecnalia (Spain). She has 10 years of experience as national and European R&D project management related to food processing technologies and preservation techniques. Her current work is focused on online monitoring techniques for quality detection of food products. She is leader of the work package of acceptance, economic and acceptance of the Picknpack European project.
Izaskun Pérez is a Senior Researcher in the Food Research Division of AZTI-Tecnalia (Spain). Her research is focused on the study, validation and industrial implementation of emerging technologies for food processing, with main expertise in the stabilisation and texturising by puffing-drying. She has participated in more than 30 public and private projects relating to novel technologies. She has previous experience in the Food Industry, as quality manager for a snack company.
Raquel Rodríguez is a Food Researcher in the Food Research Division of AZTI-Tecnalia (Spain). She obtained a PhD in in Chemical Engineering from the University of the bask Country, Spain. She has more than 10 years of experience in R&D project management, participating in more than 30 projects related to emerging food technologies. She is co-author in four scientific publications and more than 20 contributions to congress (five of them orals). Co-author in two patented methods related to the development of an on-line classification process. Her research interests are focused on the field of innovation in Food Processes by the use of new technologies (Improvement, development, optimisation, control and validation of processes in agro-food companies).
Jaime Zufía: MSc in Environmental Engineering and Water Management. BSc in Biology. He has 17 years’ experience in conducting environmental projects related to eco-design of food products, Eco-efficiency of food production, sustainability of food chain, sustainable production and food by-products and wastewater valorisation and treatment, several of them in Latin America (Ecuador and Argentina). Currently he is the Head of the Efficiency and Sustainability Department of AZTI. He is a directorate member of the Spanish integrated Organic waste Management, member of the Spanish Network on Life Cycle Assessment; and the Technological Platform for Fishing and Aquaculture.