How food and beverage manufacturers can digitalise to drive agility and product quality
- Like
- Digg
- Del
- Tumblr
- VKontakte
- Buffer
- Love This
- Odnoklassniki
- Meneame
- Blogger
- Amazon
- Yahoo Mail
- Gmail
- AOL
- Newsvine
- HackerNews
- Evernote
- MySpace
- Mail.ru
- Viadeo
- Line
- Comments
- Yummly
- SMS
- Viber
- Telegram
- Subscribe
- Skype
- Facebook Messenger
- Kakao
- LiveJournal
- Yammer
- Edgar
- Fintel
- Mix
- Instapaper
- Copy Link
Posted: 28 October 2020 | Cheryl Armand | No comments yet
Cheryl Armand looks at how businesses can best make the move to digital and achieve enhanced operational agility while keeping a strong focus on maintaining optimum food quality standards.
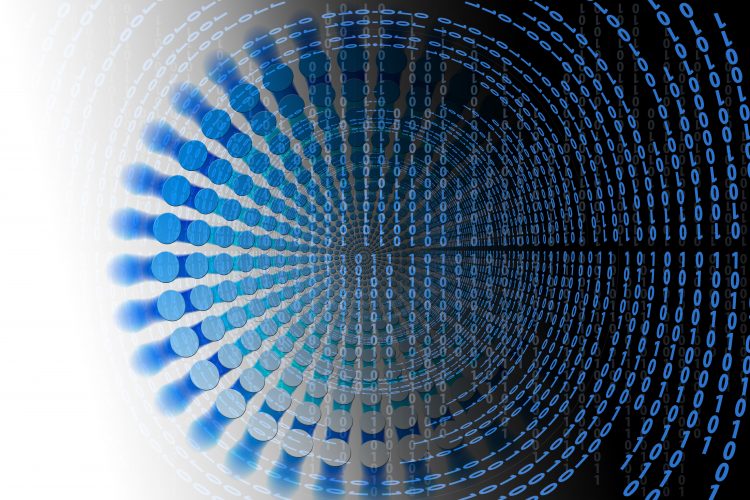
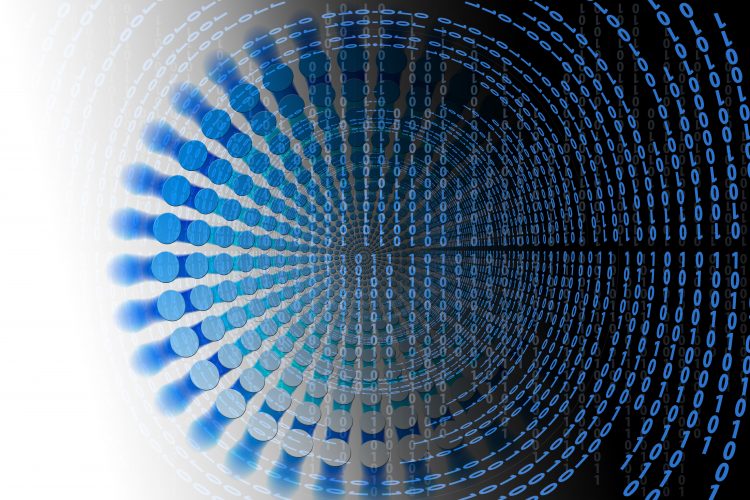
High levels of downtime, coupled with difficulties gathering and analysing data; regulatory requirements, evolving consumer preferences and supply chain demands are all driving the move to digital for food and beverage manufacturers. But choosing a strategy can be overwhelming. Many food and beverage businesses are still in the very earliest stages of their digital journey and others have tried to ‘digitalise’ with less than impressive results.
The entire process can be complex. With so many technology players trying to penetrate the industry, it can be difficult to know which path to follow. There are many tools and solutions on the market today that claim to give businesses transparent, early, accurate warnings of equipment failure or breakdown. There is plenty of contrary guidance about ways to avoid unplanned downtime and predict real-time quality. Further adding to the complexity, in the current climate, when access to many producer sites is limited, it is often difficult to know how to deploy the best technology with the least amount of operational exposure to outsiders.
Building an environment that does not break down
From the outset many manufacturers are unsure what steps to take first, which technology to adopt and how digitalisation will impact the bottom line. Some may be uncertain which products best align with their comprehensive digitalisation strategy or may even still have a need to create one, while others may have a wider range of digitalisation goals. However, the bottom line for most is a pathway to capital expenditure avoidance and an avenue to boost overall enterprise performance and profits.
As a starting point in their digital strategy, the latest asset performance management (APM) software can be leveraged to help manufacturers accomplish a plethora of goals with a rapid return on investment. APM encompasses a variety of solutions with analytics that oversee not only the equipment and process but also can help manage risk and provide a pathway to cloud connection and enterprise visualisation helping create a collaborative workflow across an enterprise.
The best such solutions offer capabilities above and beyond ‘preventative maintenance’ alone, not just incorporating early warnings of equipment failures but also prescribing detailed actions to mitigate or solve problems.
For food and beverage manufacturers, more accurate failure detection means fewer false alarms, unplanned downtime avoidance, downscaling preventive maintenance to reduced overall repair lifecycle cost and increased net production output. If producers can self-sufficiently and accurately predict time to failure, they will know precisely when and how a failure will occur and what to do about it. This allows manufacturers adequate time to schedule repairs vs. unavoidably having to address them.
From eliminating equipment downtime to driving process improvement
Another key area where APM can bring rapid value to manufacturers is in increasing overall product quality, yields and throughput. The latest multivariate analysis tools identify hidden or latent variables that inhibit organisation’s processes.
Using an offline mode, historical data can be fed into these tools along with qualified processing parameters to help create an ideal process model as a starting point for the online application. Thereafter, real-time data can be continuously fed through the predictive intelligence model and hundreds of process variables analysed. This delivers alerts to users so they can efficiently navigate unnecessary disruptions during processing. These live alerts notify operators of process drift and needed corrective actions.
This kind of solution and approach can be utilised in a variety of applications such as batch processing, product development, incoming raw material quality decision making, real-time quality prediction or overall process trouble shooting.
Digitalisation – new opportunities ahead
All of the above technologies are examples of digitalisation, which has become a buzzword for food and beverage companies in recent years. It is important to highlight also, however, that embracing digitalisation doesn’t mean replacing humans but rather it allows humans to more efficiently contribute to their organisations. It enables them to spend more time acting on insights versus trying to understand or create them. Just imagine a scenario where everyone who influences your process can agree on the best course of action based on facts vs. assumptions.
With so many technology players trying to penetrate the industry, it can be difficult to know which path to follow.
All this is part of a broader holistic approach to digitalisation that maximises performance engineering and production optimisation to balance supply and demand across a food and beverage organisation’s enterprise value chain for superior results. Yet, asset performance management tools and technologies are key to this approach and will remain fundamental in helping food and beverage companies maintain their operations, drive uptime with actionable insights and ultimately make a success of their digitalisation strategy.
About the author
Cheryl Armand is the Senior Account Manager, Food and Beverage, AspenTech, and has more than 20 years of industry experience within the F&B sector. Cheryl has a Masters in Business Administration work from the University of Houston and a Bachelor of Science in Food Science and Technology from Texas A&M University. She is a long-serving member of the Institute of Food Technologist and has been involved in other key industry related organisations, including International Society of Beverage Technologist, International & Texas Association of Food Protection, Master Brewers Association and the Dallas Dairy Society where she served as a former president.