Muddy Boots’ QC system checked more than 3 million products in 2015
- Like
- Digg
- Del
- Tumblr
- VKontakte
- Buffer
- Love This
- Odnoklassniki
- Meneame
- Blogger
- Amazon
- Yahoo Mail
- Gmail
- AOL
- Newsvine
- HackerNews
- Evernote
- MySpace
- Mail.ru
- Viadeo
- Line
- Comments
- Yummly
- SMS
- Viber
- Telegram
- Subscribe
- Skype
- Facebook Messenger
- Kakao
- LiveJournal
- Yammer
- Edgar
- Fintel
- Mix
- Instapaper
- Copy Link
Posted: 15 January 2016 | Victoria White | 1 comment
Chances are, when you walk into your local supermarket and select your fruit and vegetables, you’re choosing a product that has been rigorously QC checked by Muddy Boots’ Greenlight Quality Control software…
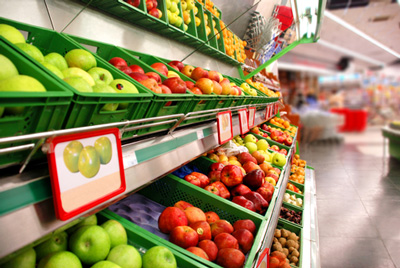
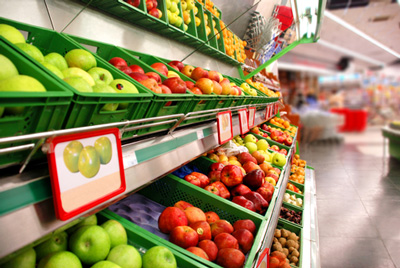
More than three million items of fresh produce were quality checked by Muddy Boots’ QC system in 2015.
That’s an increase of 140% since the horsemeat scandal surfaced in 2013. Muddy Boots says this demonstrates the urgency to rebuild consumer trust and guarantee only the safest and best quality fresh produce reach our supermarket shelves.
Chances are, when you walk into your local supermarket and select your fruit and vegetables, you’re choosing a product that has been rigorously QC checked by Muddy Boots’ Greenlight Quality Control software.
Greenlight Quality Control is widely used by around 70% of the UK’s fresh produce supply chain, as well as a growing global customer base, from supplier right through to retailer. The system works by centralising product specifications online for all members of the supply chain to easily access, update and share information instantly. This results in complete visibility of the performance of sites, suppliers and products in real-time.
The food industry has been working towards better transparency for some time, and there’s now a real sense of urgency to rebuild and maintain consumer trust and prevent food scandals from taking place.
“The vast adoption of Greenlight QC over the last couple of years in particular validates the importance of quality assurance across a supply chain. The consequences for getting it wrong can be catastrophic; damaging both sales and reputation,” states Mark Powell, Product Development Manager at Muddy Boots.
Muddy Boots to launch Greenlight QC iPad app this year
The wide adoption of Greenlight QC also comes with significant environmental and ethical benefits. Mark explains how connecting your supply chain together on a single online platform can reduce waste by up to 50%: “Traditionally, the produce would arrive at the supermarket depot and at that point the retailer either accepts and sells the goods, or rejects and discards it. This is a risky and costly approach that makes working efficiently and sustainably a real challenge.
“However, when all members of your supply chain are accessing the same data via Greenlight QC, everyone is clear on the required specification from the get-go; the supplier, and even his suppliers, have confidence that the produce is the appropriate quality for the customer before it’s shipped, and the retailer has confidence that all produce about to arrive at depot is fit for purpose.
“This early warning system allows the supplier to identify any produce that the retailer will reject before he ships it, therefore allowing him to redistribute to another customer. The end result is a significant reduction in waste, increase in efficiency, and stronger supply chain relationships,” concludes Mark.
With the launch of Muddy Boots’ Greenlight Quality Control iPad app in early 2016, the Company anticipates further growth in this system across the supply chain, as quality management becomes truly portable.
This is a great mechanism to assist in immediate decision making at the retail level for both consumers and retailers. We could add to that with a Certification logo to let consumers know that we have confirmed no adulteration or illegal substitution by DNA testing in the product.