‘Ingesting metal fragments can cause injury’ states the FDA
- Like
- Digg
- Del
- Tumblr
- VKontakte
- Buffer
- Love This
- Odnoklassniki
- Meneame
- Blogger
- Amazon
- Yahoo Mail
- Gmail
- AOL
- Newsvine
- HackerNews
- Evernote
- MySpace
- Mail.ru
- Viadeo
- Line
- Comments
- Yummly
- SMS
- Viber
- Telegram
- Subscribe
- Skype
- Facebook Messenger
- Kakao
- LiveJournal
- Yammer
- Edgar
- Fintel
- Mix
- Instapaper
- Copy Link
Posted: 19 April 2016 | BUNTING Magnetics Europe Ltd | No comments yet
In a 7 page document, the US Food and Drug Administration (FDA) highlights that metal fragments in food may cause dental damage, lacerations of the mouth or throat, or laceration or perforation of the intestine…
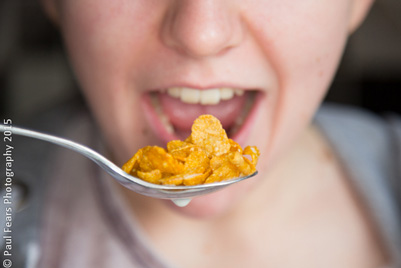
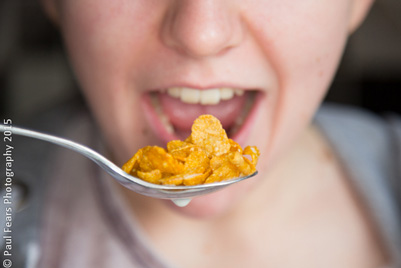
In a 7 page document, the US Food and Drug Administration (FDA) highlights that metal fragments in food may cause dental damage, lacerations of the mouth or throat, or laceration or perforation of the intestine. However, they do not mention the untold damage to a company’s reputation and the subsequent financial damages.
It is nearly impossible to stop metal fragments entering a process line. Processing equipment will wear, especially with metal-to-metal contact, and there will be equipment failures (e.g. valves, screens, conveyors, etc.). Once that fact is accepted, then a solution to the problem of removing and detecting that metal before it reaches the consumer can be found.
Several methods of metal removal are employed of which Magnetic Separation and Metal Detection are the most common. The effectiveness of this equipment is dependent on the nature of the product, the location of installation and the maintenance. Well planned and executed maintenance, especially with planned Magnetic Separator cleaning schedules, will ensure that metal separation levels are maintained for the long term.
Magnetic Separation is commonly used to remove metal from liquids and free flowing solids or powders. By positioning the Magnetic Separator in the process (i.e. inside a pipeline or chute), magnetically susceptible metal (such as ferrous metal and abraded or work hardened stainless steel) is attracted by the magnetic field and then held on the surface of the magnet. There are many different designs of Magnetic Separator and strengths of magnet to suit different applications and locations.
Baby food is just one example of a foodstuff that is generally processed in a slurry form with small sized solids. However, as with all processed foods, there is a possibility of metal being introduced into the product and it is vital that this is removed prior to bottling.
The metal contamination can be in the form of larger sized ferrous particles such as nuts, nails, screws or clips or even stainless steel that has been abraded or broken off other process plant. Also, many plants use pens and other items manufactured out of magnetic plastic. All these are attracted and captured by strong Rare Earth Magnets.
For removing metal from slurries and liquids, one of the most common designs of Magnetic Separator used is the Magnetic Liquid Trap. This has a very simple design and uses Cartridge or Tube Magnets orientated vertically down into the product flow. The slurry or liquid has to pass close to the strong magnets and through the magnetic field, thus capturing all magnetically susceptible materials.
When the product or the cleaning process exposes the magnets to high temperatures, then Rare Earth Magnets designed to operate in temperatures up to 150 degrees centigrade are recommended.
There are also Magnetic Liquid Traps especially designed for installation in processes where the product has to be kept at a high temperature e.g. chocolate. These have a ‘water-jacket’ through which hot water is pumped, maintaining the temperature of the product inside the pipe.
Metal Detection can also be used as part of a separator, whereby metal is detected and then rejected immediately. This is often used in free fall locations, but can result in high losses of product. More commonly, Metal Detection is installed at the end of the process either just before or/and after the product has been packaged and packed.
The FDA document is very helpful and even outlines ways to determine if the potential metal contamination hazard is significant. Continuous monitoring and verification form key parts of the metal contamination management plan. Regular and planned checks on the Magnetic Separators and Metal Detectors are vitally important to ensure that the level of separation and detection performance is maintained over time. Bunting offer a free annual Magnetic Separation audit, when all installed equipment is checked and tested with the results being recorded for future reference and comparison. The verification procedure includes assessing any changes to the process or product that may result in a requirement to alter the location or design of the installed Magnetic Separation equipment. The audit is conducted by a trained engineer and a verification report is supplied with details of the recorded tests, comments and recommendations. The FDA report provides advice on how to identify critical control points and how to develop a metal inclusion control strategy.
The US Food and Drug Administration (FDA) give specific guidance on the issue of metal inclusion or contamination on their website http://www.fda.gov/downloads/Food/GuidanceRegulation/UCM252440.pdf
For further information or to discuss any magnet, magnet application or metal separation application, please contact us on:
- [email protected]
- call us on 01442 875081
- Send an enquiry via our website
Related organisations
BUNTING Magnetics Europe Ltd, Food & Drug Administration (FDA)