Seals and seal design for use in the food and beverage industry
- Like
- Digg
- Del
- Tumblr
- VKontakte
- Buffer
- Love This
- Odnoklassniki
- Meneame
- Blogger
- Amazon
- Yahoo Mail
- Gmail
- AOL
- Newsvine
- HackerNews
- Evernote
- MySpace
- Mail.ru
- Viadeo
- Line
- Comments
- Yummly
- SMS
- Viber
- Telegram
- Subscribe
- Skype
- Facebook Messenger
- Kakao
- LiveJournal
- Yammer
- Edgar
- Fintel
- Mix
- Instapaper
- Copy Link
Posted: 4 January 2012 | Dr. Till Riehm, EHEDG Subgroup Seals | No comments yet
Plant operation managers are ultimately responsible for the quality of the products they manufacture. Every food item, pharmaceutical, or cosmetic product must be shipped in perfect condition and safe for humans and animals. Neither toxic substances nor microorganisms should be present at levels that could affect the product quality or shelf life, putting consumer health at risk. Therefore, facilities must be constructed to satisfy all applicable hygienic requirements, especially during running operations. The facilities must be designed for easy and reliable cleaning, especially in those areas where automatic clean-in-place (CIP) and sterilisation-inplace (SIP) processes are used and visual inspections cannot be carried out.
In this regard, seals are of special importance: first, in terms of the chemical degradation of the sealing materials, and second, in terms of their use as static or dynamic seals at all connecting points in the facility.
Material
The choice of sealing materials for use in direct contact with the products has to be made carefully. The materials are required to fulfil multiple requirements. The seal material must comply with all applicable legal regulations and should at a minimum conform to FDA (Food and Drug Administration) CFR §177.2600, EG 1935/2004, and EU 2002/72/EG, depending on where the machinery is to be used. This ensures that no substances that are known to have negative effects on the product quality or the health of the consumers are used in the production of the seal’s raw material.
Plant operation managers are ultimately responsible for the quality of the products they manufacture. Every food item, pharmaceutical, or cosmetic product must be shipped in perfect condition and safe for humans and animals. Neither toxic substances nor microorganisms should be present at levels that could affect the product quality or shelf life, putting consumer health at risk. Therefore, facilities must be constructed to satisfy all applicable hygienic requirements, especially during running operations. The facilities must be designed for easy and reliable cleaning, especially in those areas where automatic clean-in-place (CIP) and sterilisation-inplace (SIP) processes are used and visual inspections cannot be carried out. In this regard, seals are of special importance: first, in terms of the chemical degradation of the sealing materials, and second, in terms of their use as static or dynamic seals at all connecting points in the facility. Material The choice of sealing materials for use in direct contact with the products has to be made carefully. The materials are required to fulfil multiple requirements. The seal material must comply with all applicable legal regulations and should at a minimum conform to FDA (Food and Drug Administration) CFR §177.2600, EG 1935/2004, and EU 2002/72/EG, depending on where the machinery is to be used. This ensures that no substances that are known to have negative effects on the product quality or the health of the consumers are used in the production of the seal’s raw material.
Plant operation managers are ultimately responsible for the quality of the products they manufacture. Every food item, pharmaceutical, or cosmetic product must be shipped in perfect condition and safe for humans and animals. Neither toxic substances nor microorganisms should be present at levels that could affect the product quality or shelf life, putting consumer health at risk. Therefore, facilities must be constructed to satisfy all applicable hygienic requirements, especially during running operations. The facilities must be designed for easy and reliable cleaning, especially in those areas where automatic clean-in-place (CIP) and sterilisation-inplace (SIP) processes are used and visual inspections cannot be carried out.
In this regard, seals are of special importance: first, in terms of the chemical degradation of the sealing materials, and second, in terms of their use as static or dynamic seals at all connecting points in the facility.
Material
The choice of sealing materials for use in direct contact with the products has to be made carefully. The materials are required to fulfil multiple requirements. The seal material must comply with all applicable legal regulations and should at a minimum conform to FDA (Food and Drug Administration) CFR §177.2600, EG 1935/2004, and EU 2002/72/EG, depending on where the machinery is to be used. This ensures that no substances that are known to have negative effects on the product quality or the health of the consumers are used in the production of the seal’s raw material.
For example, for certain elastomeric mixtures, which must conform to the food and drug administration (FDA) CFR § 177.2600, only substances that are on an approved list defined by the FDA can be used. Then, the cured rubber has to pass extraction tests with water and vegetable oil, which represent aqueous or fatbased products. For water, the extraction limit for the first seven hour test is 20 mg/inch2. Then, the specimen is exposed to the water for an additional two hours where the extraction should not exceed 2 mg/inch2. For hexane, the corresponding extraction limits are 175 mg/inch2 for the first seven hours and 4 mg/inch2 for the additional two hours.
The sealing material has to be resistant to all processed media. Therefore, an EPDM material would be best for use with aqueous media. High quality EPDM materials have proven to be resistant to acid and basic CIP cleaning agents, to withstand steam sterilisation of up to 180°C, and work in low fat-containing media at lower temperatures. With rising fat content and elevated temperatures limiting the use of EPDM materials, the use of FKM should be investigated as an alternative material. FKM shows fairly good properties in high fat contents, but often fails during the cleaning process when exposed to alkaline cleaning agents. If resistance to aqueous media, fat, and CIP/SIP cleaning agents is required, the best choice would be a special highly fluorinated FKM (Fluoroprene). These FKMs show excellent properties in all relevant media used in the food and beverage industry, even at temperatures of up to 200°C, without having the economical disadvantages of Perfluoroelastomers (Simriz, FFKM).
A recent concern is the impact of flavouring agents on the sealing material. The problem is widely known in the beverage industry. For example, after the processing of orange lemonade, an extended rinse cycle is required before the filling line can be used again for processing pure water products. If the rinsing process is not done properly, flavouring agents like limonene will migrate from the seals and add consumer detectable taste impurities to the next production batch. Beverages with a higher content of flavouring agents, such as energy drinks, have an even stronger impact on seals. The flavouring agents have a strong impact on the sealing material, which leads to swelling of the seal’s material and mechanical weak – ening of the seal. Seal failure is only a matter of time. Highly fluorinated FKMs can be used in limited applications. Only FFKM materials will work as standard sealing materials in con – centrated flavouring agent-containing products.
Basic design principles
For the design or choice of seals used in food and beverage equipments, there are some basic principles that should be followed. Due to hygienic design, a seal should fulfil the following requirements: the seal itself should have a clean and even surface without defects, the seal should be flush with the equipment’s components to prevent dead spaces and a metal stop ensures that the seal is not over or under compressed and that the joints are centred.
A large temperature range of the processing equipment can have a severe impact on the seal and the sealing function. At higher temperatures, the elastomer expands, which might lead to protrusion of the seal material into the equipment. This is critical in terms of dead space with respect to cleaning processes and the fact that product flow might tear off sealing material, which then contaminates the product. Upon cooling, the seal material will retract into the groove. This leads to free space in the groove, where product contamination and bacteria growth can occur.
Seals for food couplings and clamp connections are standardised products with which pipes for liquid media can be easily connected and sealed. Seals for food fittings have been standardised in accordance with DIN 11851 regulations. Their extraordinarily fast and uncomplicated installation of these clamps, thanks to the ease of separating them from the flange, has made them an extremely popular choice. Clamp connections, manu – factured per International Standards Organisation (ISO) 2852 (for inch measure – ments) and Deutsches Institut für Normung (DIN) 32676 (for metric measurements), are easy-to-install solutions as well. Both options are highly economical and easy to acquire.
However, since seals for food couplings have been designed without metallic stops, seal compression can vary once the seal is installed and gaps and dead spaces can appear. A similar problem arises with clamp connections, which also fail to provide consistent compression. Further, field experience has shown that major stresses can affect the seal landings, which can cause sealing material to shear off, con – taminating the product.
A good example of a standardised accepted solution to this problem is the aseptic clamp connection per DIN EN 11864 Part 3. The European Hygienic Engineering & Design Group (EHEDG) provided their expertise to avoid the problems associated with previous connection designs and develop a reliable hygienic solution. The result: two seals, one an O-ring that has already proven its effectiveness in practice, and one a moulded part for effectively connecting pipes with operating pressures of up to 40 bar. The metallic stop provides the seal with consistent compression, and a sufficient gap is created between the seal and the product space to allow rinsing during the cleaning processes. This gap also serves as space that can accommodate volume expansion due to exposure to heat or the influence of media without producing forces that can result in material shearing. To the left and right, the sealing surfaces are directly in contact with the product space, preventing product leakage and the corresponding risk of contamination.
Examples of a hygienic design solution
The valve design used for years by a mid-sized company began to reach its performance limits due to increasing expectations and more extreme processing parameters. In certain applications, this led to frequent problems, with short product life cycles and numerous valve failures. This made it necessary to take a closer look at the double seat valve’s piston seal. The O-ring on the lower valve disk showed clear signs of material wear in one of these applications; the seal truly looked ‘chewed up’. Detailed examinations revealed that the round O-ring groove was overfilled at room temperature; when the temperature increased to 120°C; major stresses in the material were created. The motion of the valve disk led to shearing off of parts of the O-ring, creating the previously described damage.
The valve manufacturer wanted to keep the same seal, so the only viable solution was to redesign the groove. With the help of FEM analysis, the O-ring’s expansion (given the use of EPDM with an expansion coefficient of 1.6 x 10-4 1/K, friction-free) due to increased temperature and swelling was calculated. The resultant maximum principal deformations in the material are represented in Figures 1 and 2. The critical point for the EPDM material is roughly 60 per cent expansion; however, this is only an approximate value, as additional strains such as temperature are factors that must be taken into account. In this case, even the green coloured sections should be considered critical in both graphs.
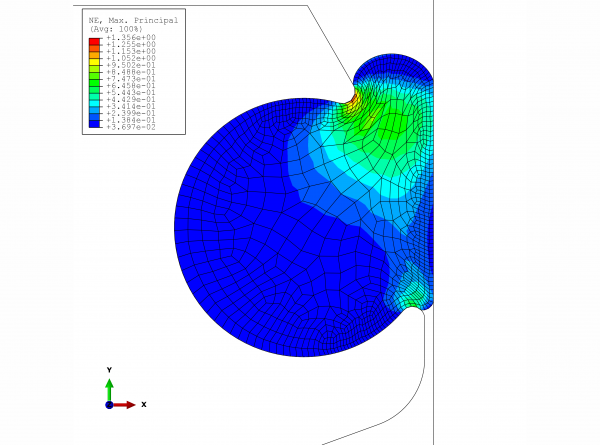
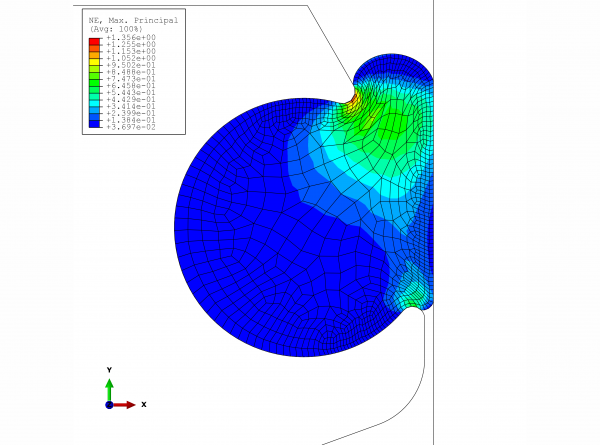
FIGURE 1Maximum principal deformation in the material in the installation situation, temperature: 136°C
The results are apparent. The O-ring seal needs more space to expand. Once this space has been provided, the new clearance should be carefully measured and analysed. At the lower extreme, the seal must be able to perform reliably despite the low level of compression; at the upper case, the forces at work should not become so high as to pose a risk of damage.
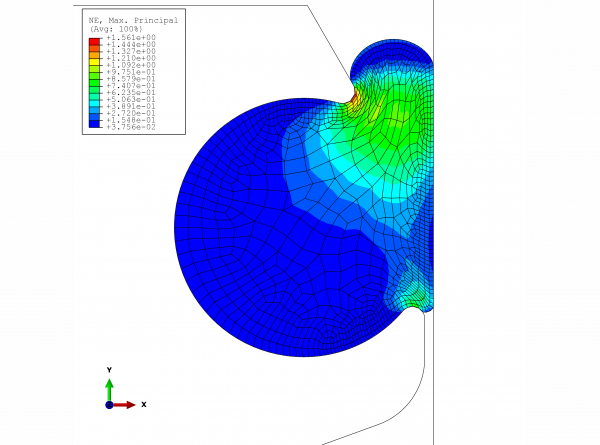
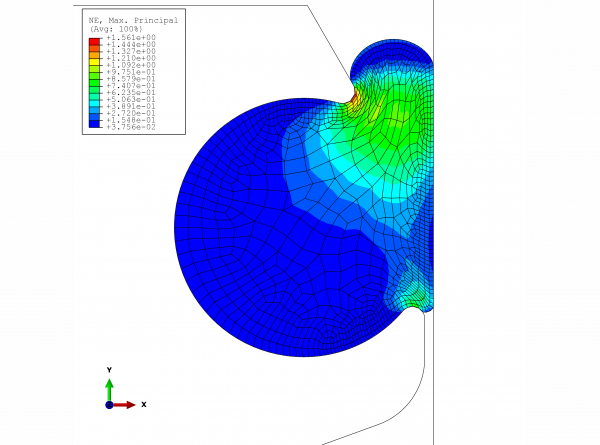
FIGURE 2Maximum principal deformation in the material in the installation situation with 3% swelling due to the influence of media
First, the lower threshold is considered, which is done by calculating the normal stresses that work on the following assumptions:
● The groove is large, but within the acceptable tolerance
● The O-ring cross-section is at the lower tolerance limit
● Pressurisation: 10 bar
● Room temperature
● No swelling due to contact with media
Figure 3 clearly shows the results of the functional testing. The problems of leakage and subsequent contamination can be readily seen. As shown in the lower right-hand section of the graphic, the effects of the operating pressure cause the seal to extrude out of the groove. This allows the product (and potentially microorganisms) to collect in the gap space created. To avoid this problem, the sealing location must always be directly on the product space.
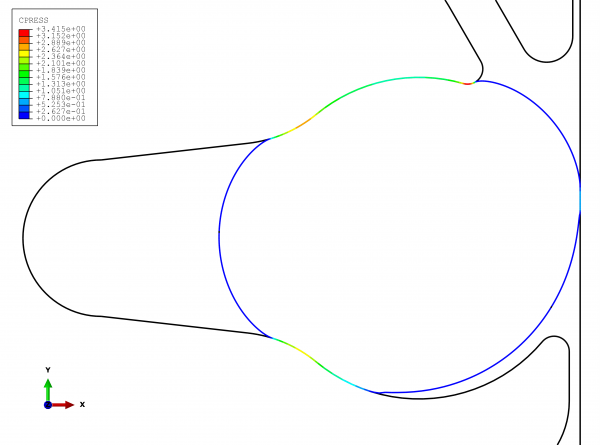
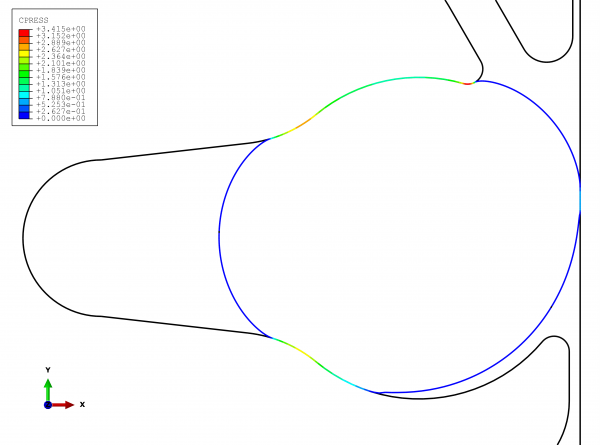
FIGURE 3View of the sealing locations with the improved geometry with expansion space (note: This is not the actual solution)
It is equally important to simulate the upper extreme, where the most important question is: can the seal hold up? Figure 4 shows the results for the following parameters:
● The groove is small, but within the acceptable tolerance
● The O-ring cross-section is at the upper tolerance limit
● No pressurisation
● Temperature: 136°C
● Swelling due to contact with media: three per cent In the new, optimised groove, the sealing locations are directly on the product space. At a temperature of 136°C and simultaneous three per cent swelling due to contact with media, the elongation reaches 70 per cent. As this strain occurs in only a small area and several stress factors must be taken into consideration at the same time, the expansion value is acceptable.
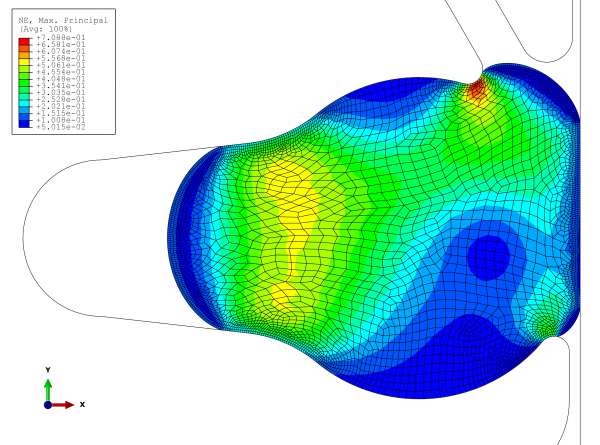
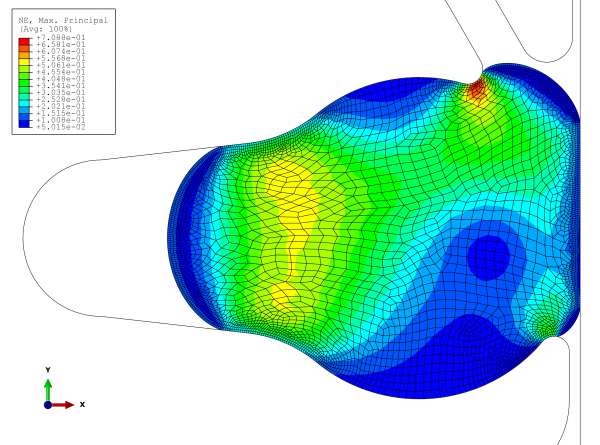
FIGURE 4 View of the maximum strains at work in the elastomer
Conclusion
The sealing component is often an undervalued part. The seal is often considered a C-part, but its functionality is as critical as the functionality of an A-part. The choice of material and design of the seal is therefore crucial for the quality of the products produced and the lifetime of the processing equipment. For all applications in the food and beverage industry, the con – sultation of sealing specialists is recommended as, for example, one EPDM material is not at all similar to another EPDM material and the different behaviour of these two materials might lead to serious problems. For all custom specific parts, the sealing specialists will focus on hygienic design, as they are highly trained and experienced in this field.
Biography
Dr. Till Riehm has worked for the Freudenberg Group since 2008. He started his career at Freudenberg in the Central Research & Development Department where he was responsible for projects focused on improved surface properties of elastomers. During that time, he developed several new coatings to reduce the friction and wear characteristics of sealing components. He then took a position with Freudenberg Process Seals, the seals and gasket specialist for the processing industry in the Freudenberg Group, where he was responsible for the pharmaceutical industry. Currently, Dr. Riehm is Head of Marketing and Business Development at Freudenberg Process Seals.